Research shows that fleet companies waste approximately half of the money they spend on traditional equipment maintenance. Getting started with AI-based predictive maintenance will not only save you money in the long run, but also reduce vehicle downtime and increase customer and driver satisfaction.
The transportation industry is already heavily investing in Artificial Intelligence. In 2017, the global AI market in this sector amounted to $1.4 billion, and it is expected to reach $3.5 billion by 2023. It is further encouraging to know that transport and logistics is among the industries that benefit from using AI and ML solutions the most.
Continue reading this article to understand what predictive maintenance is and how deploying Artificial Intelligence in transportation can benefit your business.
What Is Predictive Maintenance?
Following the conventional approach to maintenance, owners would examine their machinery during pre-scheduled repair sessions based on manufacturer recommendations, rather than equipment status. They would replace old parts, even when they were still in working condition. However, age-related maintenance is not always the best choice.
The problem with this approach is that it doesn't consider other relevant factors. For example, operating conditions can be different from the manufacturer’s expectations. As a result, some parts may be damaged faster or serve longer than the manufacturer specifies. A study by ARC Advisory Group found that only 18% of assets fail due to age-related issues. The other 82% of malfunctions are random.
Predictive maintenance (PdM) implies understanding the "health" status of a machine to determine if it needs repair. To examine the device in detail, the maintenance team installs sensors to measure a multitude of parameters, such as vibration and temperature.
The Traditional Approach to Predictive Maintenance Was Challenging
In the early days, connecting a range of sensors to asset management software was a costly procedure reserved for critical equipment. For the rest, technicians walked around with collectors gathering sensor data. This approach has several limitations:
- It is labor intensive and time consuming
- Failures could occur in between data collection rounds
- There wasn’t real-time overview of the machinery performance data
- Hard-to-access pieces of equipment were not examined
- Technicians conducted manual analyses, which were prone to error
Here Is Why Predictive Maintenance Is Thriving Now
Predictive maintenance, as we now know it, emerged with the 4th industrial revolution. It is based on data-driven decisions and real-time machine monitoring. The following factors mainly facilitate PdM adoption:
- The spread of wireless connectivity, which in turn serves the Internet of Things
- Advances in AI
- Cloud computing is now secure, robust, and inexpensive
IoT sensors transmit equipment data in real time. AI algorithms study this data and identify abnormal behavior, which indicates that a component will fail soon. Spotting the defects at early stages gives equipment owners the time to schedule maintenance and stock replacement parts.
According to McKinsey, such an approach to predictive maintenance reduces equipment downtime by 30-50% and increases its lifetime by 20-40%.
How Does the Transportation Industry Employ AI-Based Predictive Maintenance?
The traditional approach to fleet management was to take vehicles out of rotation every 4,000 miles (approximately) for regular maintenance, which was often unnecessary. AI-enabled predictive maintenance allows owners to make repair choices based on the vehicle's current condition, not on pre-scheduled time intervals. It is not surprising that predictive maintenance is gaining popularity in the transportation industry.
"From winterization practices to aftertreatment systems to maintenance intervals, we have used the data to influence our actions and drive lower downtime for our customers."
Cindy Crawford, Group director of maintenance at Ryder
AI built into dynamic dashboards helps spot recurring issues and drivers with the most problematic "driving styles." It will also enable the maintenance team to prioritize machines for maintenance.
Furthermore, incorporating AI in the logistics industry will support technicians developing prescriptive maintenance plans.
"For example, detecting that certain asset conditions, such as tire pressure levels combined with other factors such as distance traveled lead to specific maintenance issues, an intelligent prescriptive maintenance plan can be tailored to optimizing the maintenance cost and performance of individual assets."
Tony Summerville, Founder and CEO of Fleetio
Predictive Maintenance in Action
Even though predictive maintenance is still in its early stages, there are several compelling examples of Artificial Intelligence in logistics and transportation.
Uptake Helps Its Clients Reduce Unplanned Maintenance
Uptake is an industrial AI software company serving customers from the logistics and transportation industry. It has worked with North America's largest fleets and claims to have reduced its clients’ unplanned maintenance by 7-10% and fuel costs by 2-3%. Uptake uses telematics data transferred by trucks, such as battery cranking voltage, and combines it with contextual information (e.g., weather and traffic data) and historical fleet data.
The company processes all this data with its AI models to view a vehicle's condition, predict any malfunction possibilities in the future and notify fleet managers of a potential failure well in advance. The notification period ranges from ten days to one month, allowing managers to decide whether to address the problem directly or let the driver safely complete their trip and deal with the warning later.
Trenitalia Decreases Maintenance Costs by Monitoring Its Trains
Trenitalia is the primary train operator in Italy. The company deployed a dynamic maintenance management system, which combined IoT, AI for transport and logistics, and in-memory computing to optimize maintenance of their trains.
Before this initiative, trains relied on regular maintenance after reaching particular mileage milestones. To minimize unnecessary repair shop visits and unexpected breakage, the company applied predictive maintenance to the essential parts of their rail vehicles. As a result, the technicians could monitor their fleet round the clock. They could improve inventory management and reduce maintenance costs by up to 8%.
Benefits of AI in Transportation and Logistics:
Automates analytics
AI alleviates the burden of data analysis from fleet operators and delivers useful insights.
"There are 17,000 fault codes that can be broadcast over the J1939 connector and each one could indicate up to 25 different failure modes. AI stitches together all the data points from disparate sources to create actionable insights."
Braden Pastalaniec, Head of Fleet AI at Uptake
Reduces vehicle downtime
For some fleet companies, vehicle downtime equates to $448-760 in lost revenue per day. Organizations can significantly decrease this by incorporating artificial intelligence into their transport systems and analyzing truck data to spot potential malfunctioning. This will eliminate mileage-based maintenance altogether.
Minimizes fuel waste
Proper vehicle maintenance saves fuel. An AI logistics system can help detect pressure differences between the inlet and outlet, which can happen when the filter is clogged. That way, the vehicle owner will have the chance to replace the filter before the vehicle’s monitoring system sends Diagnostic Trouble Codes (DTC).
Getting Started with Predictive Maintenance
If you are convinced that incorporating artificial intelligence-based predictive maintenance into your logistics system will result in saving time and money, here is how to proceed:
Gather different types of data
Start by installing sensors on your vehicles' board to gather telematics data such as harsh braking or acceleration, fuel consumption, idling time, etc. Note that for comprehensive analytics, you will also need contextual data, e.g., weather conditions. Additionally, keep track of the maintenance you already performed and its cost profiles.
Use flexible cloud technologies for data storage
Trucks consist of many components supplied by different manufacturers, and they generate about four gigabytes of data a day, which is challenging to store and access. Flexible cloud architecture can facilitate integrating third-party services if needed, while cloud computing can help process massive datasets and access data from everywhere, anytime.
Integrate this new system with the rest of your enterprise applications
Integrate the new tool into your existing enterprise asset management (EAM) and data warehouse to create a unified view of your affairs and trigger a workflow of related activities.
Incorporate user-friendly dashboards
As predictive maintenance systems typically contain enormous amounts of data, it will be useful to add a visual representation. Using a dashboard with customizable functionality, fleet managers can view the data they are most interested in at a given moment. It is worth considering a cross-platform representation so that employees can access the data on their work computers and smartphones.
Promote the new culture
Predictive maintenance will bring change to the transportation industry, and managers need to make sure that everyone is on board. Since the early 1900s, when the first diesel engine was installed in a truck, drivers have been following the same pattern: the truck malfunctions, they tow it in, and fix it at a repair shop. Their mindset will have to change to accept the idea of proactively repairing a part that has yet to fail.
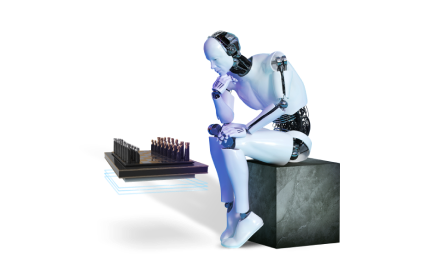
Maintenance Is Better than Repair
With the increasing availability of the Internet and IoT services, the transportation industry has several possibilities to improve its operations. One such opportunity is predictive maintenance. It can decrease the vehicle's downtime, help efficiently stock spare parts, and even guide technicians through the repair process.
To fully benefit from PdM, you will have to go through some internal changes. But it doesn't stop there. The whole transportation ecosystem will need to adapt. One example is that manufacturers will have to adjust their warranty requirements to accommodate replacing compromised parts that haven’t failed yet.
These changes will take time. Meanwhile, bypassing the warranty to replace a part that will eventually break might still be cheaper than taking the truck out of rotation later on. Maintenance is already better than repair.
More articles on the topic
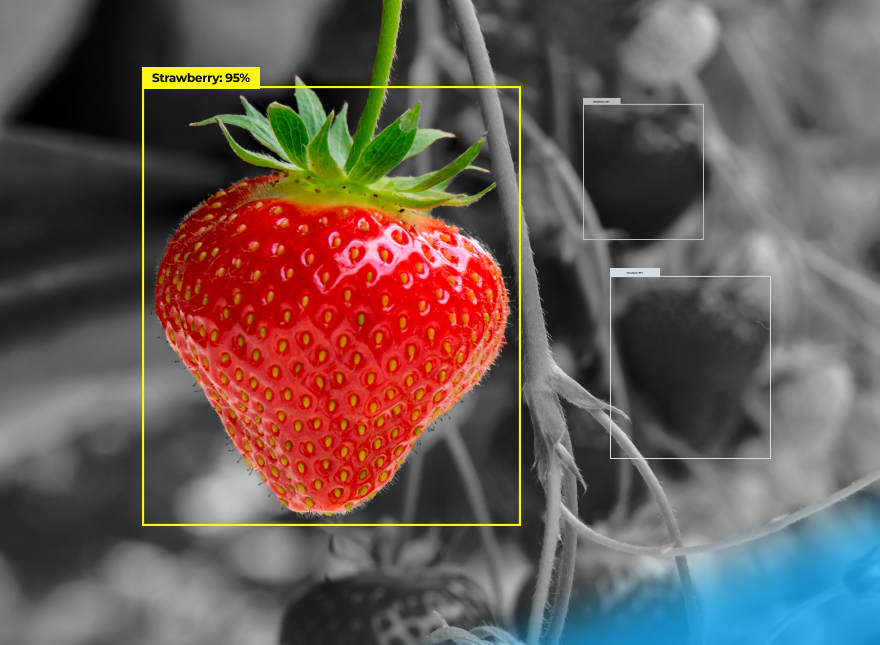
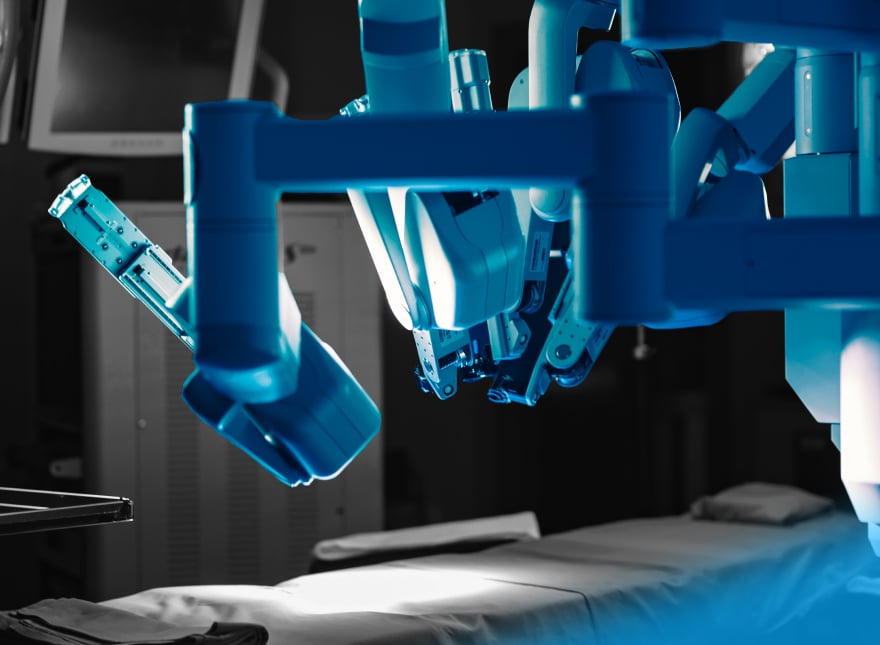
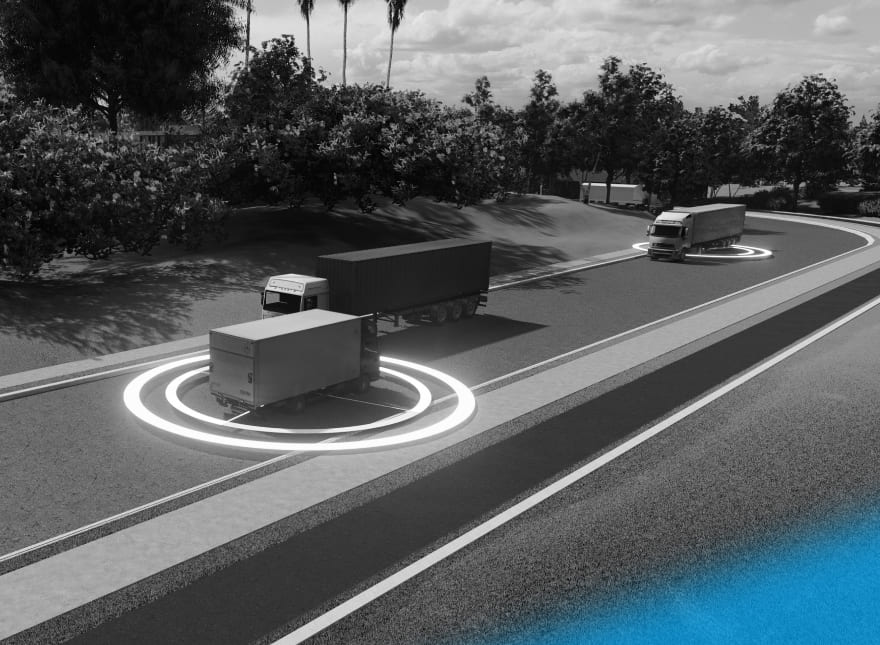
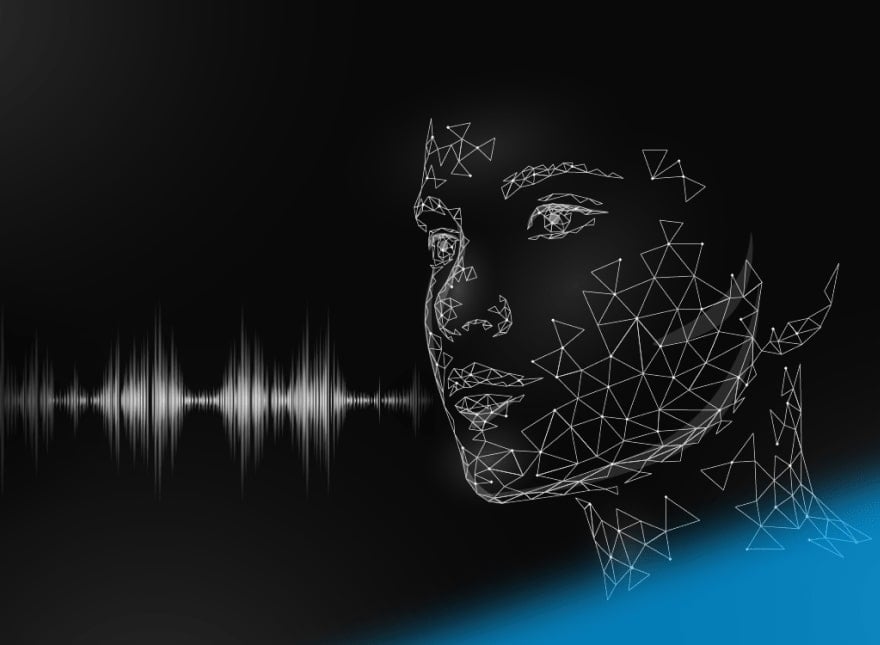
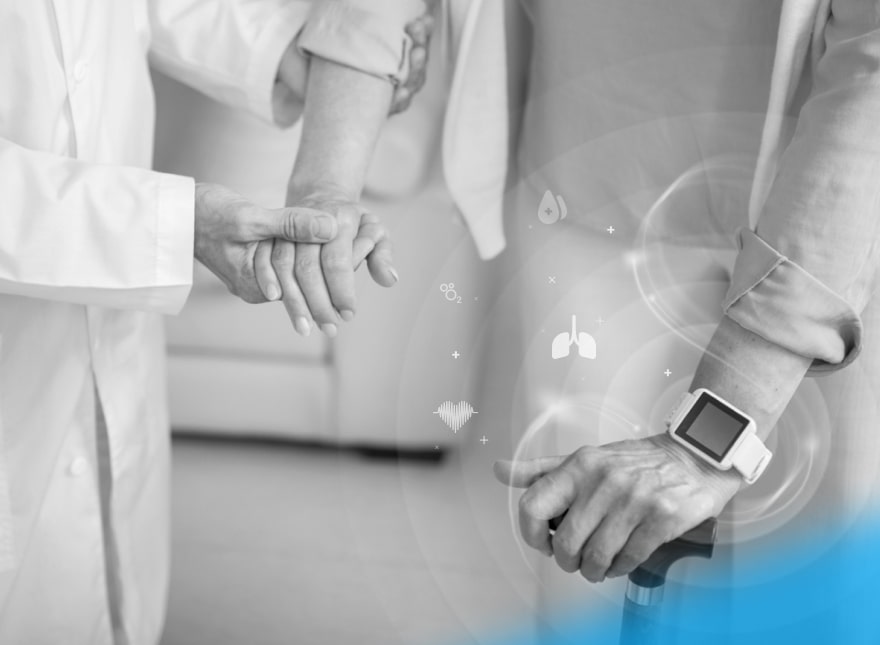
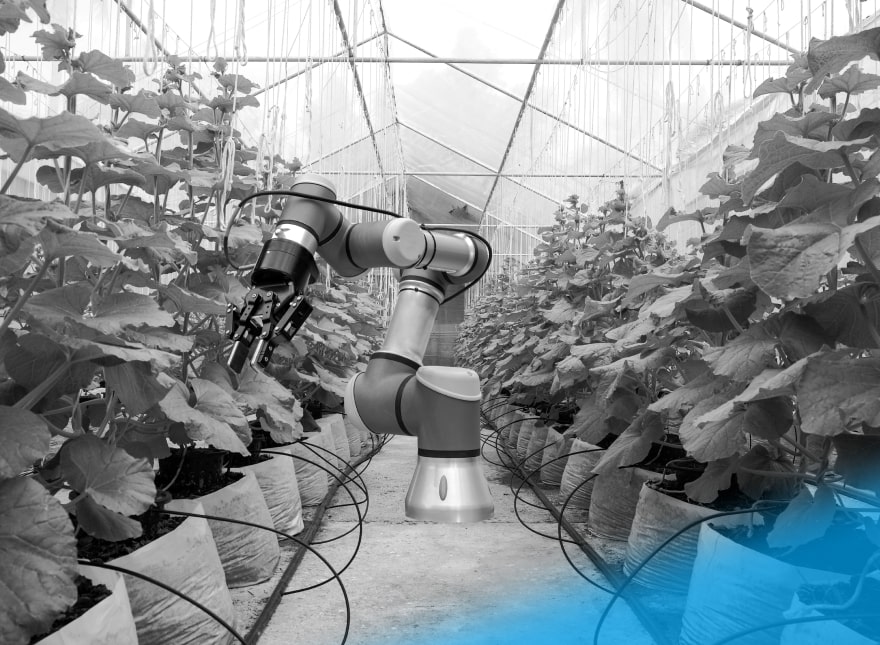