Large construction projects run 80% over budget and 20% longer than estimated. Who are the guilty parties here? You may point to the lack of resources and unqualified staff on site. But these aren’t the only culprits. When equipment—a tower crane or a grader—breaks down, becomes misplaced, or even gets stolen, it negatively affects the project time, the budget, and the man-hours involved. Deploying IoT in construction helps prevent this.
IoT is a game-changer for construction: it not only cures its most common pain points but also disrupts the industry. The technology can enhance on-site safety, increase staff productivity, reduce delays, and even support environmental sustainability. Take a look at the most promising areas for deployment.
Why Deploy IoT for Construction Equipment
The construction industry adopts new technologies as easily as carrying a bag of rocks. There are many reasons, including the use of traditional building practices, old dump machines that need retrofitting, and the underinvestment in digitalization. You know there are many more instances to add to this list.
In the meantime, going digital to manage and maintain construction industry solutions adds robust perks in terms of safety, process optimization, and business decisions. Here are some common scenarios when deploying IoT for construction equipment becomes both a tactical and strategic solution.
Improving Safety on Site
Traditional methods of promoting workers’ safety proved their inefficiency. In 2019, one out of five worker deaths happened in construction (across industries, a total of five thousand workers died in the US). This share was the same in 2018. Emerging tech has the capability to change this.
One proven solution is wider adoption of smart wearables. Traditional safety helmets, clothes, and footwear protect workers from fatal and non-fatal outcomes that have already occurred. Helmets or exoskeletons with embedded sensors and attached tags, in turn, prevent accidents and provide proactive safety monitoring. How? They collect biometric and geolocation data and warn about related health hazards.
Another cure is digitalization of heavy trucks. Imagine two machines. One version is a traditional aging forklift doing its job on a construction site. Human error plays a significant role here because this is a worker who has to keep track of what's going on around them. The responsibility to prevent the accident is on people. The other machine is a smart truck equipped with a 360-degree antenna that is able to detect workers in the forklift zone and alert or even stop the truck to avoid accidents. No wrongful deaths here.
Optimizing Processes
As a construction company, you can leverage IoT to prevent delays through monitoring and controlling staff productivity and truck efficiency. A study from Caterpillar shows that the use of IoT in earthmoving activity allows for consuming 40% less fuel, working 36% less, and completing each project stage 40% faster. Isn’t this what you need?
Look how it all works with equipment, for example. Sensors attached to equipment and their parts monitor usage and maintenance data. Operators through dedicated apps get automated alerts on machinery status and see when repairs are required. Some tools can even schedule service appointments. With IoT on site, it’s convenient to monitor specific conditions of heavy machines like humidity, temperature, and pressure and make immediate improvements or schedule appointments when something goes wrong. So, IoT solutions make it possible to effectively maintain, repair, and support heavy machines and dedicated software.
Smart Prediction
Unplanned downtime may cost a fortune, so you definitely want to avoid it. How can IoT help? It can collect data from sensor-rich trucks and send it to the cloud. There, AI interprets data, doing it faster and more accurately than humans. For example, it’s possible to feed algorithms with datasets collected from the equipment and train machine learning models to predict asset failure or downtime. So, IoT development helps construction companies predict and prevent issues and thus make data-driven decisions on project planning, using resources, and improving performance.
IoT-rich predicting helps save drastic amounts of both time and money. Findings from another industry—manufacturing—prove this. According to Deloitte, IoT-based predictive maintenance services can reduce the time required for maintaining equipment sometimes by half. This way, it adds an hour or two of uptime to each working shift and saves you up to 10% on maintenance expenses.
4 Types of IoT Solutions for Heavy Machines
Asset Tracking
This allows construction companies to control their fleet of heavy machines at multiple sites. With IoT, you connect thousands of equipment pieces. And thanks to GPS technology, your on-site and remote workers can track location and performance of each asset in real time. Geofencing can help figure out how often and how long workers use any of the machines. It’s convenient to analyze wear and tear and plan repairs or calculate the cost for renting. Additionally, a virtual map can present a vivid view of all construction assets. Planning reallocation of heavy equipment has never been so easy!
Protecting costly machines is another convincing reason to deploy IoT in the construction industry. Loaders, backhoes, tractors, bulldozers, and forklifts are the most appealing construction equipment for criminals in the US because of their high resale value. According to the National Insurance Crime Bureau (NICB), the annual cost of equipment theft ranges from $300 million to $1 billion. With IoT on board, it’s possible to track the location of assets, get instant alerts if any is taken off-site, and even automatically shut down costly trucks when they leave the designated area.
Benefits
With IoT advances tracking and managing of assets on site, construction companies:
- Ensure more efficient and cost-saving use of assets with real-time data and the possibility to control utilization and profit
- Reduce man hours by automating the process of machine tracking
- Keep equipment highly functional and safe
- Shorten time for construction
Remote Operations
IoT in construction makes dump machines smart enough to operate remotely. While forklifts, pallet trucks, or pump trucks load, unload, and transport goods, sensors and cameras can help humans track progress by controlling and adjusting machines in real time. What about risky areas? IoT-rich remote management makes it possible for trucks to work in polluted or dangerous conditions without a man on site.
Benefits
Look at just some potential benefits of remote operations with IoT:
- Automating construction activities
- Providing all stakeholders with the opportunity to control the building process remotely
- Allowing machines to operate in hazardous areas without humans and reducing the number of workplace injuries
Safety Management
Hard hats, steel-toed boots, and safety glasses protected workers for decades. Today, IoT wearables are bringing protection to the next level. What you can have now are smart caps, smart vests, and smart eyewear. It’s possible to go even further with security on site and connect workers’ wearables with construction equipment. Sensors ensure heavy trucks detect users nearby, while workers get instant alerts on approaching machines.
Benefits
Smart safety management solutions help construction companies in:
- Keeping employees safe by reducing the number of accidents and hazards on site
- Preventing project delays
- Saving budget for insurance payments
- Avoiding reputation damage
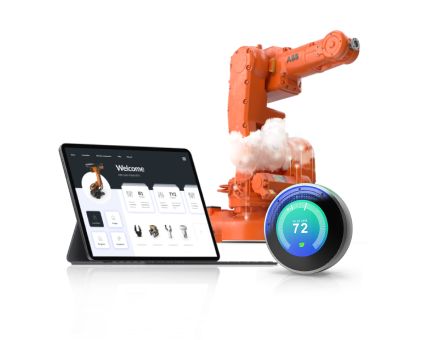
Predictive Maintenance
Deploying IoT for costly heavy tracks will let you see abnormalities before they cause failures. Sensors attached to heavy equipment can collect data about various parameters like temperature, humidity, and vibrations. Dedicated applications can help alert about possible troubles. Data from smart trucks available within reach also help technicians control wear and tear of machinery. It’s convenient not to run out of schedule for repairs and have some fixes on hand.
Benefits
Here are the major possibilities that construction companies get when they switch to IoT:
- Making more accurate predictions about assets needed/available for upcoming projects
- Reducing operational costs associated with equipment that needs repairs
- Identifying performance issues before they cause downtime
- Saving money on costly unplanned downtime
- Enhancing risk management and preventing missed deadlines
Key Takeaways
IoT turns dump heavy machines into smart devices. The technology makes possible smart asset tracking, performance monitoring, and efficient use of the machinery and allows heavy vehicles to store and share the data. The benefits of IoT in the construction industry include the following:
- Keeping equipment functional and safe
- Automating the process on sites
- Delivering projects on time and on budget
- Enhancing safety of employees
- Making data-driven predictions
- Eliminating human mistakes
At the same time, stepping on the IoT side requires you to find a trusted сonsultant to go through a strategic business change and a robust tech effort to implement multiple technologies. You may face complex technical challenges on the road. For instance, deciding how to deal with limited wireless communication on site and ensure seamless connectivity. But Softeq is here to help you make the process of IoT adoption smooth, effective, and affordable. So are you in?
More articles on the topic
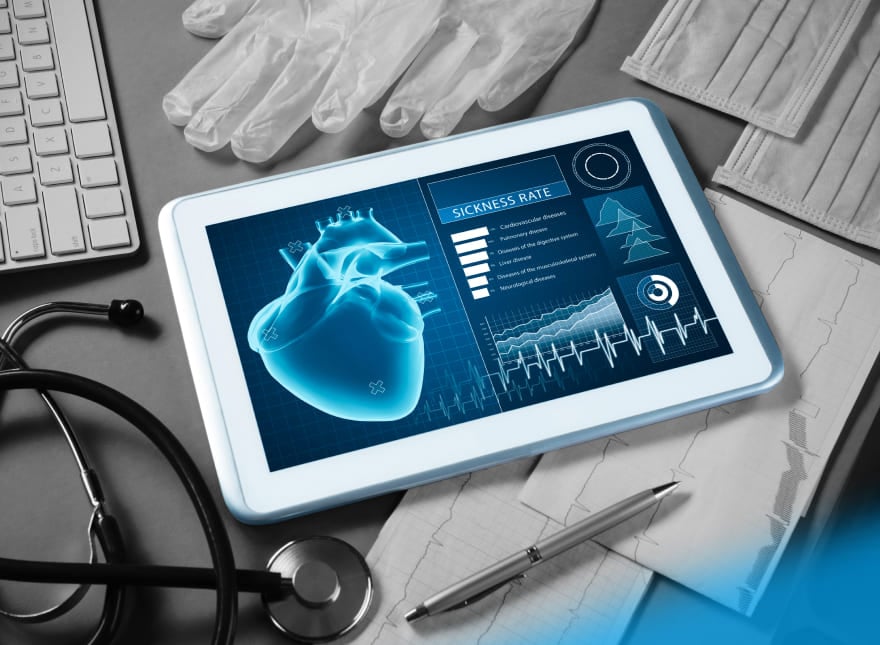
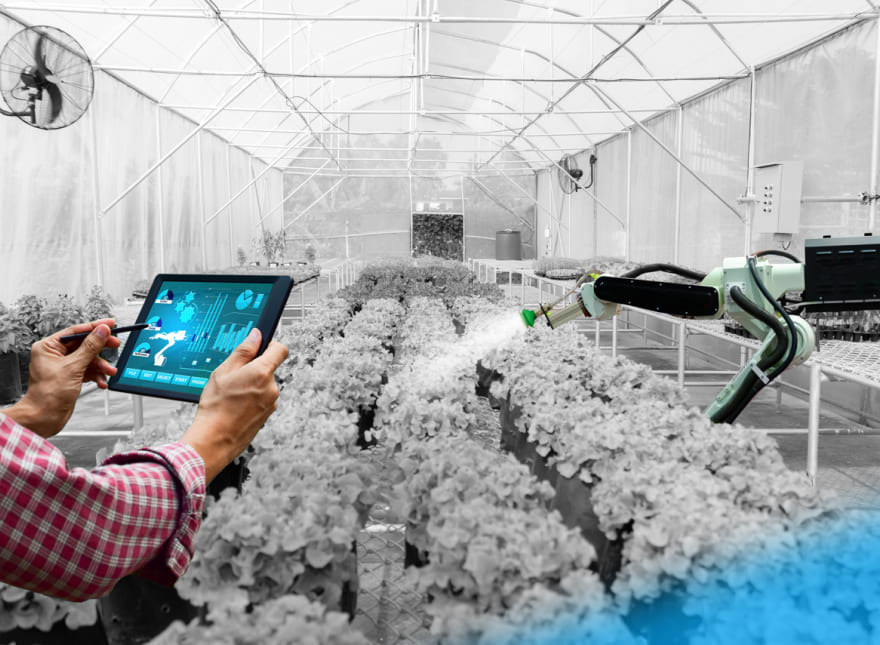
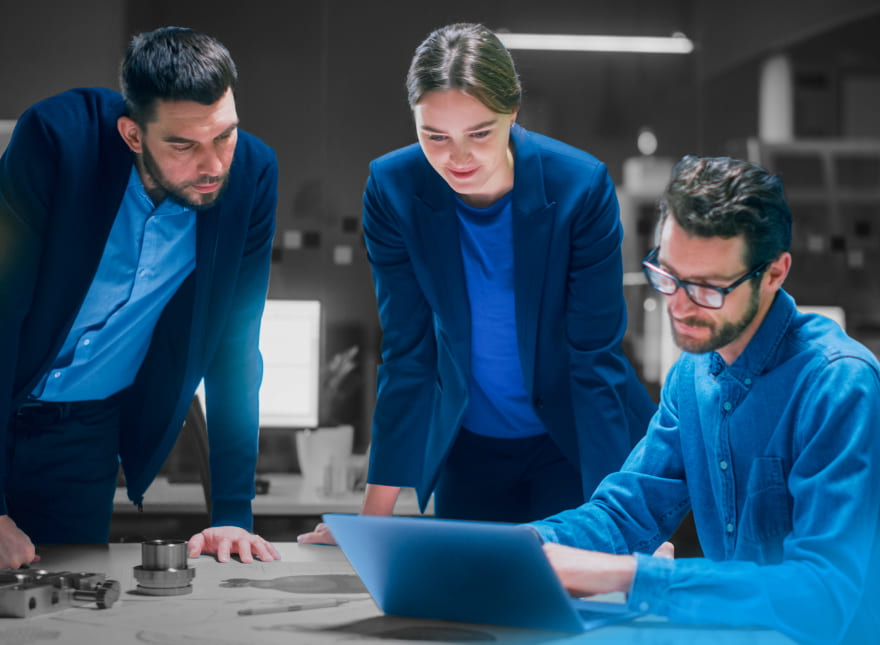
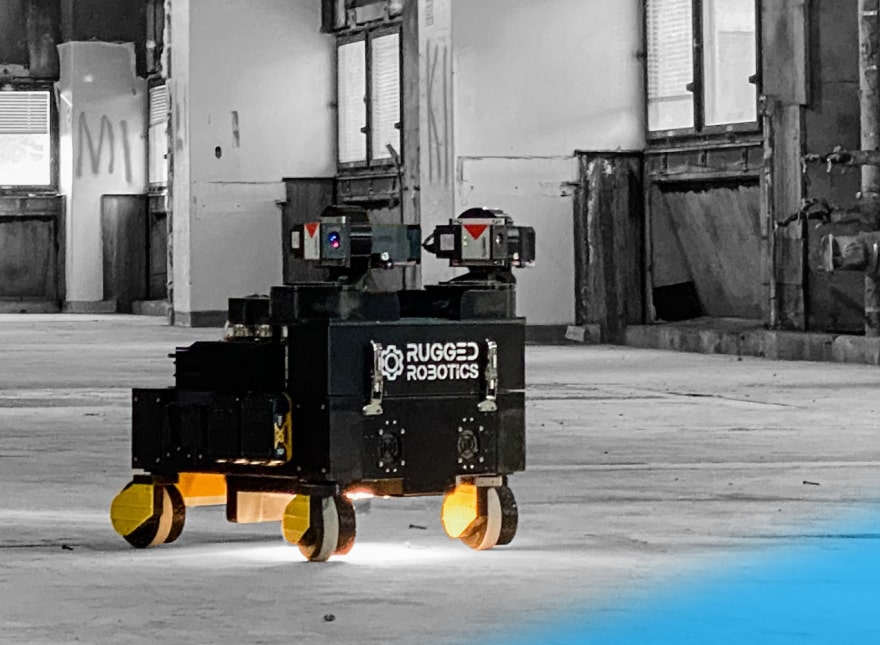
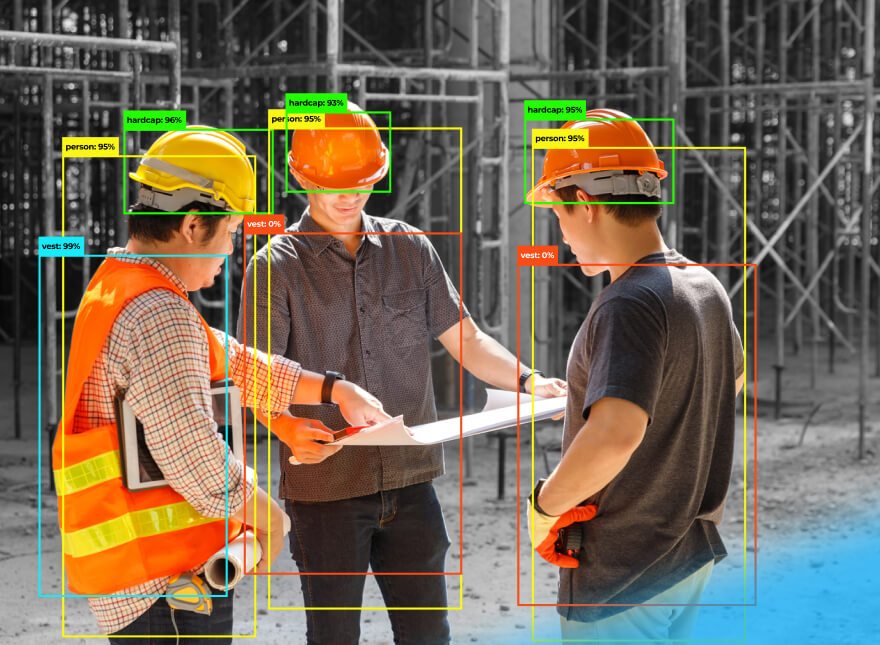
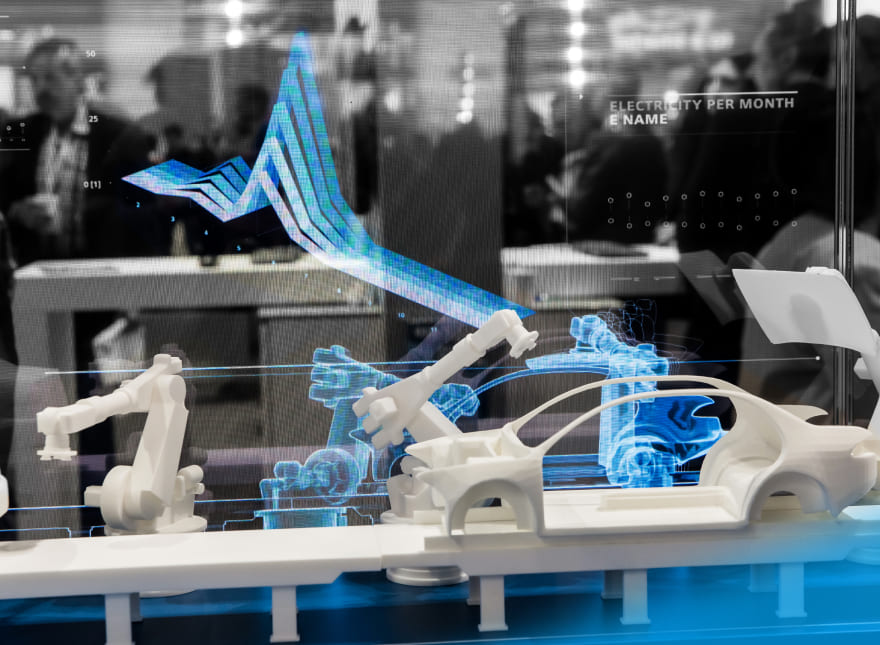