Errors in design can be very expensive. As the rule of 10 says, it costs 10 times as much to correct an error with each next production stage. Even if the design seems perfect, there’s a chance that something won’t work on the physical model. It’s even worse if the error goes undetected until after production has been completed.
But what if you were to test different designs in a risk-free environment by creating their digital twins? Firstly, early testing will help you avoid expensive reworks. Secondly, the sooner the product enters the market, the sooner you start making a profit.
In this article, we’ll cover this and other digital twin manufacturing use cases. Each features a real-life example of how companies use digital twins and benefit from the technology.
Digital Twin Applications in Manufacturing
In our recent article, we explained this technology and talked about how it works. In short, digital twins are digital duplicates of physical objects. At a basic level, they can collect data on physical objects for future use. At an intermediate level, they can simulate what-if scenarios. At an advanced level, digital twins can detect an abnormality and suggest or initiate corrective actions.
Digital twin applications in manufacturing cover all business areas of a manufacturing company:
- Pre-production. Companies can use digital twins to test different designs and component behavior.
- Production. Digital twins help manufacturers find an ideal production run and schedule the manufacturing process.
- Post-production. Companies can provide predictive maintenance or equipment training to their customers. Manufacturers can even supply them with discontinued spare parts. They can also offer product-as-a-service business models.
Let’s take a look at the seven use cases of digital twin manufacturing with real-life examples.
Use Case 1: Pre-production. Avoiding Design Errors
In traditional product development, a physical prototype goes through a build-test-redesign-retest cycle. This means the prototype is first sent to a lab for testing. This will reveal design flaws that require a rework. The trouble is that each cycle like this increases costs and stretches the development schedule.
Digital twins help remove unnecessary loops in the design optimization process. Using this technology, companies can test product design in a virtual environment. As a result, they reach the perfect design much faster.
Real-Life Example: Digital Twin in Product Development
Tronrud Engineering is a Norwegian machine manufacturer. They wanted to build a new packaging machine that works at twice the speed of the current model. To achieve that, they needed to evolve from pneumatic to full electric operation. That meant fundamental changes in design.
The company used a digital twin to design and test the product in a virtual environment. This allowed their designers, engineers, and programmers to work on the project simultaneously. As a result, programming, design, and assembly time was reduced by half!
Benefits at a Glance
- Reducing time-to-market due to fewer design errors
- Avoiding costly reworks
- Enabling testing without causing any damage
- Accelerating the development of innovations
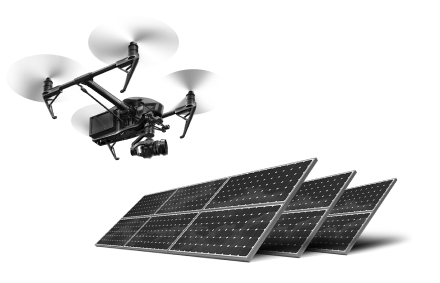
Use Case 2: Pre-production. Finding a “Golden Batch”
Finding an ideal production run that will work as a template is a challenging task. Parameters like materials, equipment, labor, space, and costs all affect the output. That’s why, in order to find their “golden batch”, companies need to keep a keen eye on how these elements influence each other.
A digital twin is a go-to solution for such tasks. Using them, companies can simulate different parameters until they find the perfect combination for manufacturing. As a result, companies can avoid quality issues and rejected batches.
Real-Life Example: Digital Twin in Pharma Manufacturing
One pharmaceutical organization (NDA) was looking for a “golden batch” for their new medicines. They set up machines manually, and as a result, more than 10,000 tablets in each trial were rejected. In addition, they had to bear the cost of disposing of the scrapped tablets.
The company applied a digital twin to find the perfect machine setup. Using simulations, their operators achieved the tablet weight, thickness, and hardness that was required. As a result, the company minimized waste and saved $900K. They also reduced the time it took the operator to set up equipment by 67%.
Benefits at a Glance
- Avoiding quality issues
- Reducing waste
- Minimizing machine setup time
Use Case 3: Production. Scheduling the Manufacturing Process
Manufacturing scheduling might seem easy. However, it’s actually more than just inputting some data into the system. There’s a multitude of factors that affect the schedule, including delayed delivery of materials, machine breakdown, and changed supplier priorities.
Some companies rely on their ERP system and Excel spreadsheets. Adjusting data in Excel spreadsheets is a tedious manual process, so exporting it is always a headache. Unlike traditional planning solutions, a digital twin represents a system that is continually updated.
Real-Life Example: Better Decision-Making in Production Planning
Lagor produces ferromagnetic cores for power transformers. Each core can weigh up to eight tons. During production, materials remain on steel pallets. These pallets move between the different workstations using roller or shuttle conveyors. The pallets are never removed from the line, even if they are empty.
They initially scheduled manufacturing lines manually. This resulted in situations where objects on the production line were creating blockages. To remove them, the company needed to unload the cores by crane and reset the whole line. But when they decided to scale up their production, it was time to make a change.
This is why the company opted to use a digital twin. They used it to model different core types, production cycles, and production plans. This helped them avoid unnecessary movements that caused bottlenecks. As a result, production became more efficient.
Benefits at a Glance
- Using the production site and equipment more efficiently
- Enabling faster delivery times
Use Case 4: Post-production. Enabling Predictive Maintenance
In 30% of cases, companies maintain their equipment too frequently. This leads to budget waste. Manufacturers specify the intervals at which their machines require maintenance, of course. But machines operating under different conditions require different maintenance schedules. This makes it difficult to set a manufacturing schedule correctly. If a machine requires maintenance more often and this goes unnoticed, it can cause downtime and, as a result, expenses.
Digital twins use sensors to continuously monitor the machine’s operation and estimate the system’s health. By applying AI, digital twins can predict how the system will behave in the future. Companies can rely on these insights to optimize their maintenance activities. This helps reduce costs, since parts are replaced only when they need to be.
Real-life Example: Flight Engine Maintenance
Rolls-Royce creates a digital twin of each of their aircraft engines. In this way, they can track how each engine flies, including its health and environmental conditions. They then simulate different maintenance regimes based on this data. If an engine has had quite an easy life, the company will extend the period between maintenance activities. If a plane operates in Qatar, for example, maintenance will be needed more often because of the sand in the environment.
With digital twins, Rolls Royce only replaces parts that actually need replacing. In some cases, this has increased the time between maintenance activities by up to 50%. On the other hand, if any of the engines need maintenance earlier than usual, this will also be identified.
Benefits at a Glance
- Avoiding excessively frequent maintenance activities
- Keeping the equipment operating for longer without interruptions for maintenance work
- Identifying when equipment requires repair work ahead of scheduled maintenance
Use Case 5: Post-production. Providing Equipment as a Service
Manufacturing companies like equipment-as-a-serviсe models (EaaS), where they pay only for the use of equipment and machines. By opting for this model, they can shift their spending from a capital expense to an operational expense. This results in more liquid capital for other needs and fewer unexpected expenses, such as repair costs. And if they don’t need the equipment, there’s no need to pay for it.
In turn, the equipment provider takes care of maintenance and other activities related to the machine’s operation. Digital twins are a good fit here. By tracking the product’s health in real time, you’ll know when it’s time to maintain the machine. This will prevent your customers from having to deal with breakdowns.
Real-Time Example: Providing Equipment as a Service
SKF is a manufacturer of bearings and seals. They decided to provide rotation services instead of selling the equipment. Their clients pay to use assets and benefit from guaranteed uptime. The fee they pay covers the provision of bearings and seals, as well as lubrication and condition-monitoring.
To provide this service optimally, SKF use digital twins. The technology evaluates the equipment’s health and registers early signs of failure. This could be balance changes, temperature increases, or vibration variations. This helps SKF engineers replace the faulty equipment before it causes expensive downtime.
Benefits at a Glance
- Increasing revenue and avoiding additional expenses
- Enabling customers to avoid high financial risks
- Increasing customer loyalty
- Ensuring machine uptime
Use Case 6: Post-production. Offering Customer Training
If you produce complex equipment, employee training is likely to be expensive for your customer because it has to be done in a real environment. But this means downtime for their core business since it takes longer for the equipment to become operational. Plus, new employees will always need training.
How about helping your customers complete training while the equipment is still in production? Digital twins make this possible because they replicate the real equipment. They can also simulate emergency scenarios, which is not possible with real equipment.
Real-Life Example: Digital Twin for Marine System Training
ThyssenKrupp Marine Systems produce surface ships and submarines. They use a digital twin to create a training environment for their customers.
The company built a virtual ship that completely corresponds to the original. The solution helps crews improve their spatial knowledge on board as they can practice operating the ship in everyday situations. Companies can also simulate emergencies, like the failure of the automation system.
The solution not only makes the teams more capable of acting under immense stress and time pressure, but it also means training can go ahead without the real vessel. This comes in handy when the ship is at sea or still in production.
Benefits at a Glance
- Training a customer’s employees even when the real equipment is unavailable
- Helping a customer avoid downtime and the associated costs
- Simulating emergencies
Use Case 7: Post-production. Providing Discontinued Parts
If a machine or piece of equipment was built decades ago, it might be challenging to maintain. Imagine an equipment manufacturer who provides their machines as a service. According to the model, the company carries out timely maintenance, which implies the availability of spare parts. But when a machine becomes obsolete, it gets discontinued. The same happens with its spare parts. Re-producing them can be unprofitable because the manufacturer has to deal with high storage costs.
However, there is a way to extend the life of aging machines: create their digital twin, including a virtual database of spare parts. With this model, you can 3D-print the part you need on demand, which will cost less than running production lines.
Real-Life Example: Digital Twin for Additive Manufacturing
In 2017, Nissan launched the Heritage Parts program. The goal is to provide owners of vintage car models like Skyline and Silvia with maintenance services. This meant the company had to produce spare parts that were no longer mass-produced. Soon, the carmaker found that storing discontinued components and molds was expensive and inefficient.
To solve the problem, Nissan decided to change their inventory management by using digital twins. They created a virtual model of discontinued parts in order to 3D-print them. Now, the company can produce spare parts on demand rather than producing stock in anticipation of future customer orders.
Benefits at a Glance
- Producing spare parts that are long out of production
- Giving aging equipment a second life
- Reducing dependence on parts suppliers
- Providing maintenance to customers even if spare parts have been discontinued
To Sum Up
Companies can enjoy the benefits of digital twins in manufacturing at every stage. In the design phase, they can avoid costly mistakes. During manufacturing, they can prevent bottlenecks and the rejection of products. In the post-production phase, they can generate revenue by offering services to customers.
If you plan to transform your business using digital twins, we’re up for the challenge. Our engineers can help you track high-value assets, automate manufacturing processes, and increase production capacity with IoT and AI. Contact us to learn more about our services.
More articles on the topic
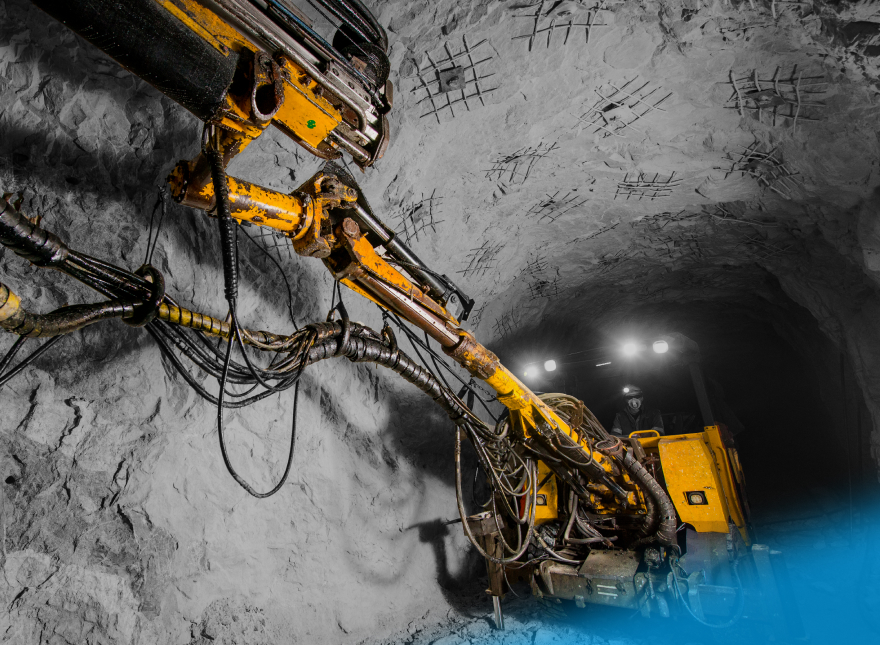
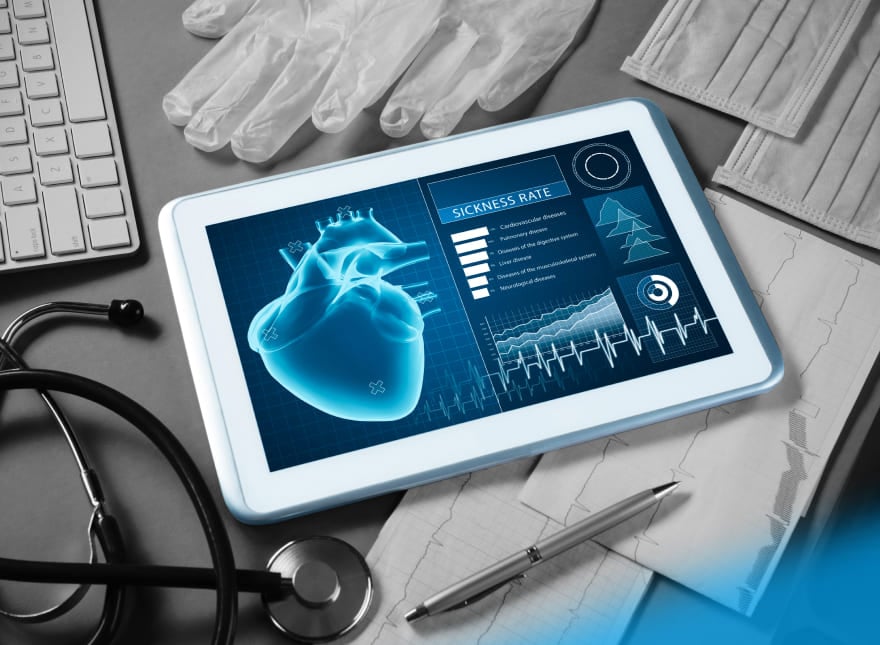
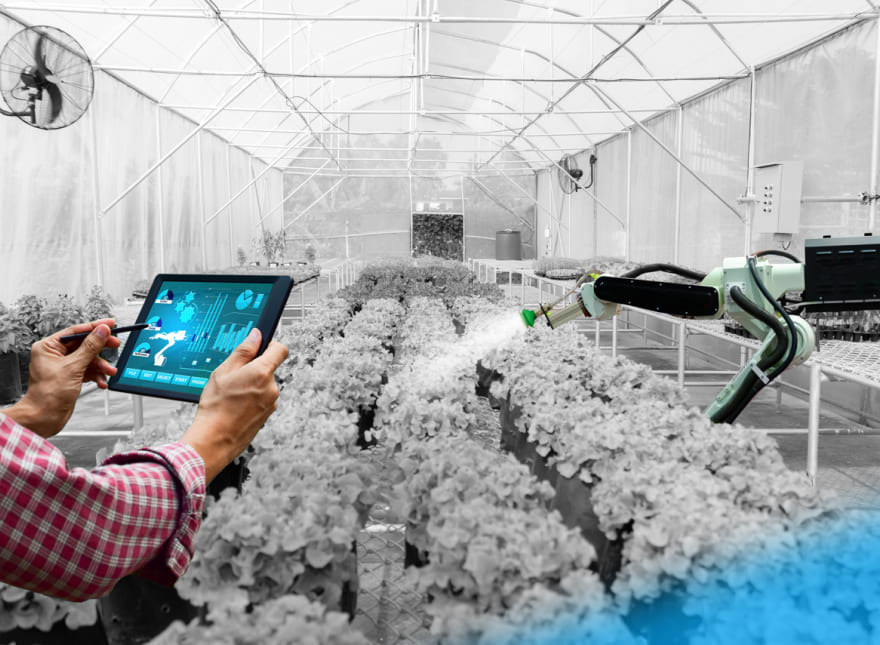
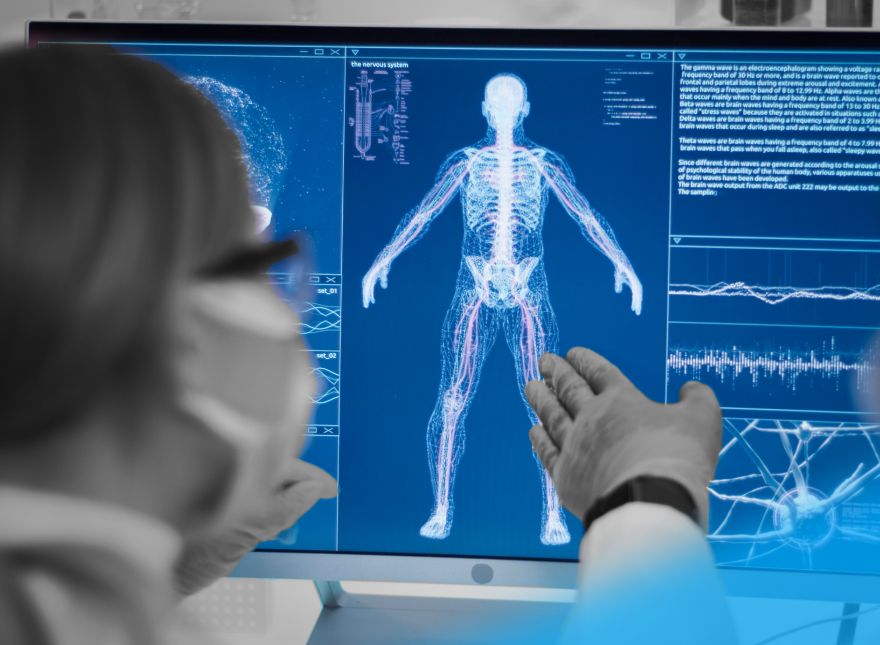
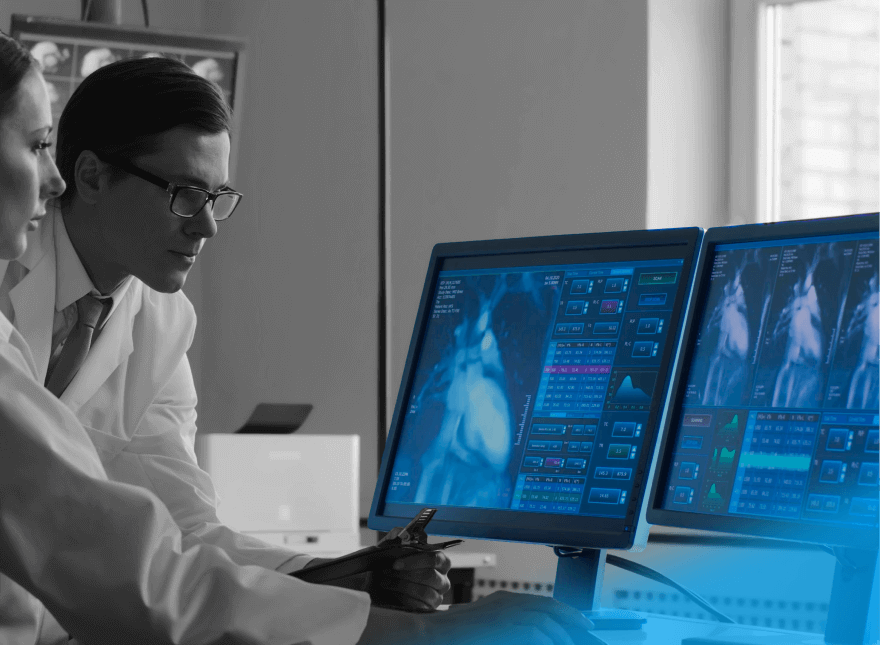
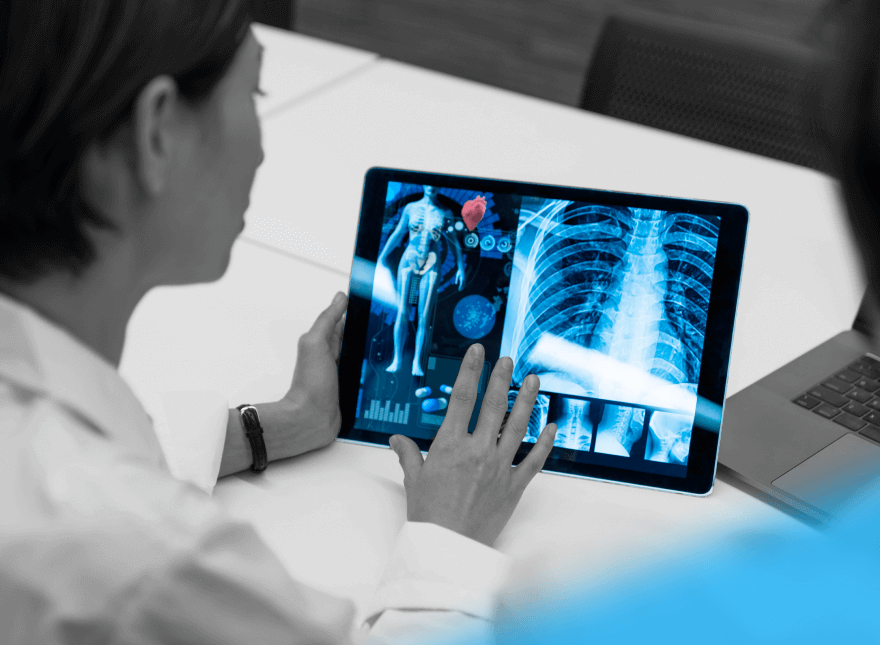