Connected solutions in the real estate industry have been around for years. They have been reported to minimize energy consumption, add new capabilities, and provide superior tenant services. However, a high cost has so far hampered their mass adoption among commercial, industrial, and residential facilities.
Emerging affordable technologies and advancements in the Internet of Things (IoT) accelerate the automation process: they help drive down costs, improve energy efficiency in commercial buildings, support environment-friendly practices, and create superior occupant experiences.
How does IoT streamline energy efficiency improvement in commercial buildings, and why do IoT solutions for HVAC play a major role in their transformation?
HVAC in Commercial Property: Challenges and Consequences
According to a technology review issued by the US Department of Energy, the residential and commercial buildings sector accounts for about 74% of electricity use and 40% of all U.S. primary energy use.
Heating, ventilation, and air-conditioning (HVAC) systems are just a small part of the commercial building infrastructure. But it takes an enormous amount of energy to condition air and then distribute it throughout a building. As a result, HVAC systems are responsible for up to 60% of the total power consumption of the building.
This happens for a number of reasons:
- A question of priorities. Building operators frequently manage HVAC systems through trial-and-error adjustments in reaction to occupant comfort feedback and relegate energy savings to a much lower priority.
- Difficulty monitoring an HVAC system. HVAC is a complex infrastructure composed of multiple elements. If a single element breaks down, the whole system doesn’t perform well. For example, a dirty air filter makes HVAC systems work harder in order to over-compensate for the hindrance in air flow, which makes system breakdown inevitable in the long run.
- Lack of regular HVAC maintenance. Real estate owners, in private or commercial property, tend to put maintenance on the backburner — if it is not broken, why fix it? — and postpone routine maintenance until it is too late. However, proper tune-ups help identify upcoming problems at an early stage, optimize the performance of HVAC units, and finally prolong the lifespan of the installed appliances.
- Incessantly shutting AC units off and on. A common myth is that you shouldn’t turn the AC off when you leave a building to avoid a strain on the system. However, when the AC is left on, it invokes unnecessary expenses and wasted energy.
As a result, commercial building owners have to deal with the consequences:
- High electricity bills. As heating, ventilating, and air conditioning are responsible for up to 40% of energy consumption, it’s no wonder that irrational electricity usage, improper refrigerant charge, and duct leaks lead to spikes in electric bills.
- Malfunctions and broken equipment. Improperly functioning equipment leads not only to high electricity bills caused by heating and cooling loops. Extra resources are spent on, first, identifying the reason for such an increase in energy consumption, and second, on repairing the equipment.
- Adverse environmental impact. The energy sector is highly dependent on fossil fuels. Excessive extraction and combustion of fossil fuels results in multiple negative effects, including air pollution and climate change.
- Occupant discomfort. Traditional thermostats control the condition of a space to a given temperature, but don’t consider changing conditions such as humidity level, airflow, sunlight, heat from office equipment and drafts, and the individual’s activity level. However, in large buildings occupants can’t just adjust the thermostat, and need to initiate a work order, contact the building superintendent, and wait for adjustments.
IoT helps the energy sector transform from a centralized system to a distributed, smart, and integrated energy system, which enables fast computations and efficient decision making. Today, lower technology costs and the increasing availability of wireless technologies are making it easier than ever to cheaply obtain sensor readings for various HVAC components. On top of this, recent advancements in data storage and cloud computing allow building operators to access the multitude of HVAC data points, such as temperature, pressure, flow rate, and gas concentration. Let's check out three major use cases of how IoT transforms HVAC systems.
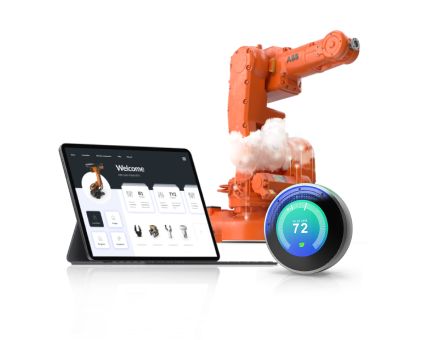
Use Case 1: Smart HVAC Control
Smart building HVAC controls help optimize the amount of conditioned (i.e., heated or cooled) air supplied throughout a building. Smart controls optimize airflow using data provided by CO2 levels, occupancy, temperature, humidity, duct static pressure, and air quality sensors and modulate the amount of airflow in one area without starving or over-ventilating another.
In the Pacific Northwest National Laboratory (PNNL) case, the institution equipped rooftop units (RTUs) with advanced controllers featuring a multi-speed fan, economizer, and ventilation controls. The evaluation found approximately 50% electricity savings for RTUs.
Use Case 2: Controlling Multiple Zones
Most commercial buildings employ a multi-zone system, which makes it harder to optimize the use of conditioned air. There are two ways to perform such control:
- Building a multi-zone variable air volume (VAV) system, where sensors are installed in each area to more effectively condition them separately from each other
- Installing a constant air volume (CAV) system served by a single unit, which makes control options less flexible: the system doesn’t exercise zone control and turns off the airflow on the whole floor
The Adobe company has chosen the VAV-based approach to air conditioning and heating in their headquarters. The office was divided into so-called neighborhoods: if any of them remained unoccupied for more than 15 minutes, the HVAC system in the neighborhood automatically shut down.
Adobe achieved a 65% reduction in energy consumption, despite a simultaneous increase in the number of their employees.
Use Case 3: Fault Detection and Diagnostics
HVAC systems face leaks, blockages, and deterioration on a regular basis, which leads to natural degradation of the system over time. To detect and prioritize faults early on, IoT-powered HVAC systems come equipped with automated Fault Detection and Diagnostics (FDD) functionality, that includes a combination of sensors and algorithms.
Modern FDDs can not only show that something has malfunctioned in an HVAC system but also determine the exact problem and its cause.
For example, Microsoft had 2 million data points at its Main Campus in Redmond, Washington, which consists of 125 office buildings. The data produced was merged into a single output, which laid the groundwork for massive predictive maintenance. As a result, maintenance checks that used to take weeks could be done in a few minutes. Overall, Microsoft realized energy savings of about 10% per year. As a result, 48% of the detected faults were corrected within 60 seconds.
IoT-based HVAC Solution Architecture Explained
A typical deployment architecture includes the following elements:
- HVAC sensors, including temperature sensors, motion sensors, light sensors, etc
- Actuators that take electrical input from sensors, transform the input into action, and act on the devices and machines
- A wireless sensor network that sends data to the gateway and to the cloud
- A gateway that enables data to be routed into the smart HVAC system and establishes bi-directional communications from the device to the gateway, and from the gateway to the cloud
- Cloud resources that enable management of the collected data from the sensors
- Embedded devices, such as mobile phones and tablets, that allow users to access and manage the HVAC appliances remotely
Here's how it works as a network:
- HVAC software interprets information from a variety of sensor points and maintains the received information in real time in a cloud-based system
- The system is connected to the analytics platform in the cloud, where data is filtered, accumulated, and shared
- Built-in algorithms use the database information to empower preventive maintenance and optimize the monitoring and control of the HVAC system
- The software generates dynamic alerts once it spots abnormal behavior, such as power consumption that exceeds the baseline defined by the system managers
These advanced controls can optimize HVAC consumption in unoccupied building zones, detect and diagnose faults, and reduce HVAC usage during times of peak energy demand.
Wrapping Up: Tips to Maximize the Efficiency of IoT-enabled HVAC Systems
- Plan out detailed HVAC system development. At the project’s outset, it is always reasonable to identify clear use cases for each of the connected sensors and IoT devices. Will the users be able to remotely control multiple standalone HVAC systems at once? Will a mobile app control only one type of equipment (e.g., a thermostat), or will it also connect with the others: ceiling fans, water heaters, and so on? Will the mobile app support both iOS and Android devices?
- Think about remote control right from the start. If the Internet goes out or a product’s battery dies, the system should be able to perform local control and feature a solution for local storage and updates.
- Don’t skimp on security. Developers of successful IoT-based HVAC projects take a zero trust approach from day one and never leave it as an afterthought. Security protocols should protect every link and every element of the system, as well as data flows to and from the connected device itself, the cloud, and the mobile and web app. Role-based access control (RBAC), end-to-end data encryption, and device status monitoring are only some of the multiple approaches, which a skillful IoT developer can include into the system.
- Ensure over-the-air (OTA) updates. To continue improving the HVAC system after installation, think through adding OTA communication, which allows IoT product development companies to modify the system without undue delays, add new features, and update the firmware on the installed HVAC devices.
More articles on the topic
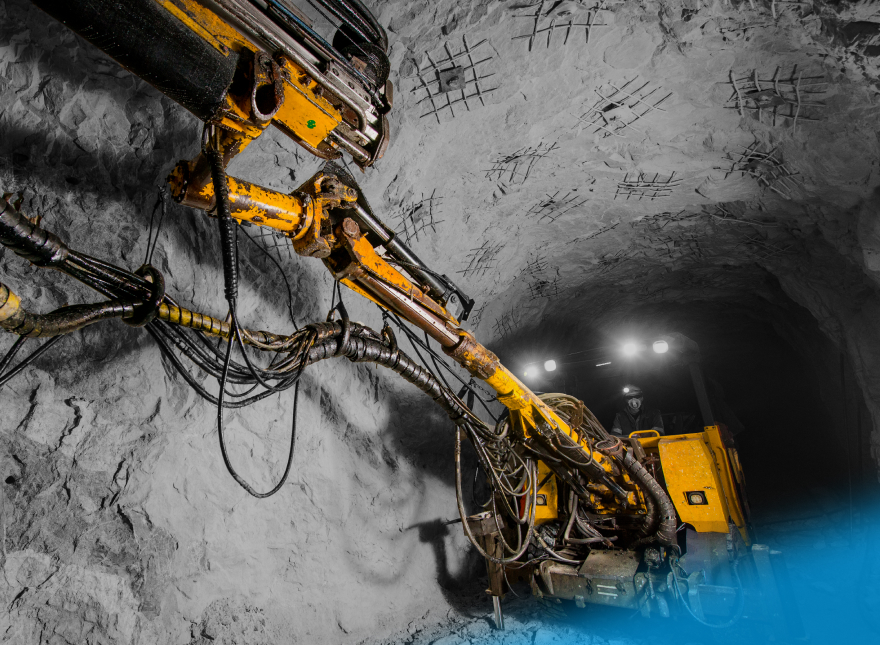
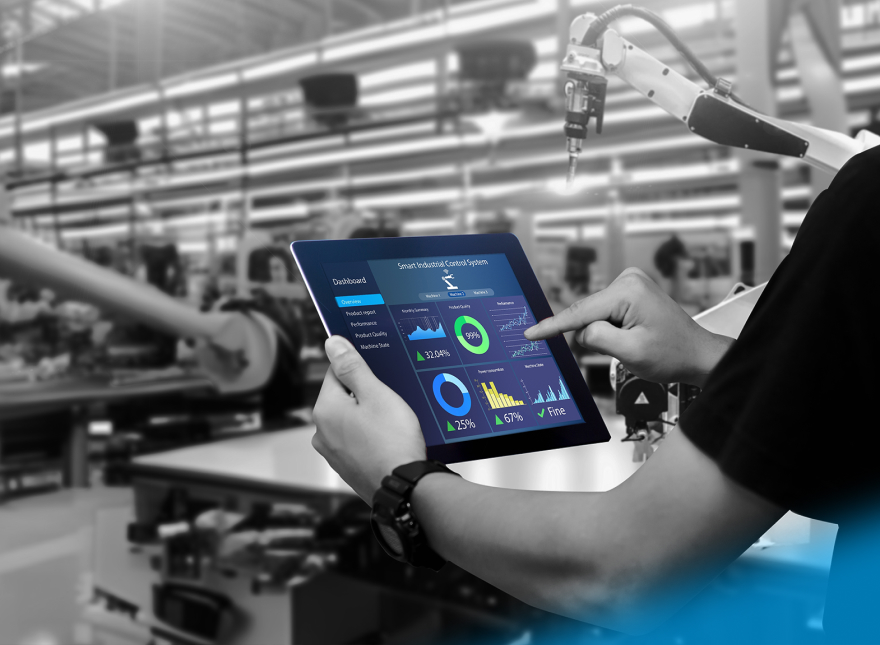
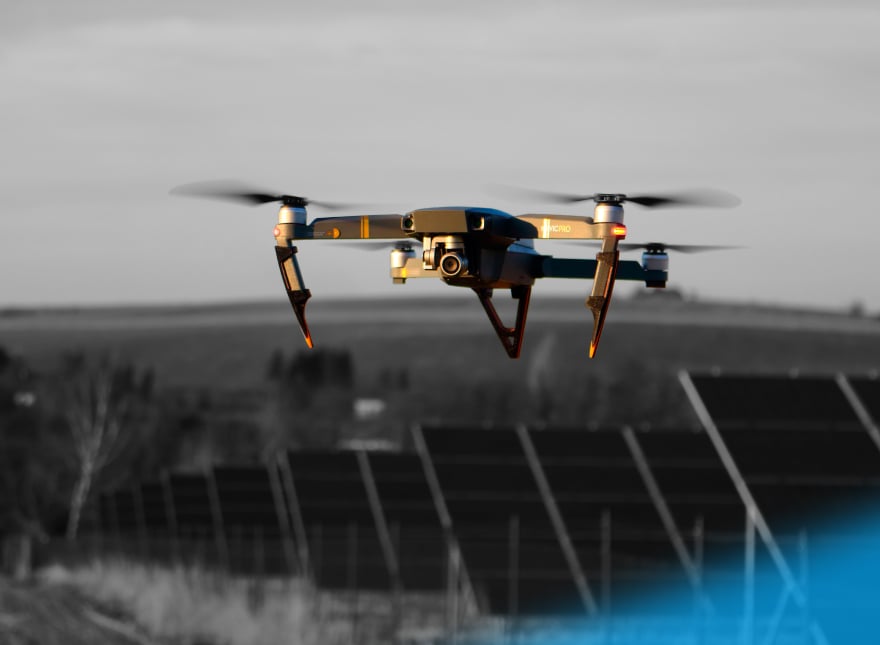
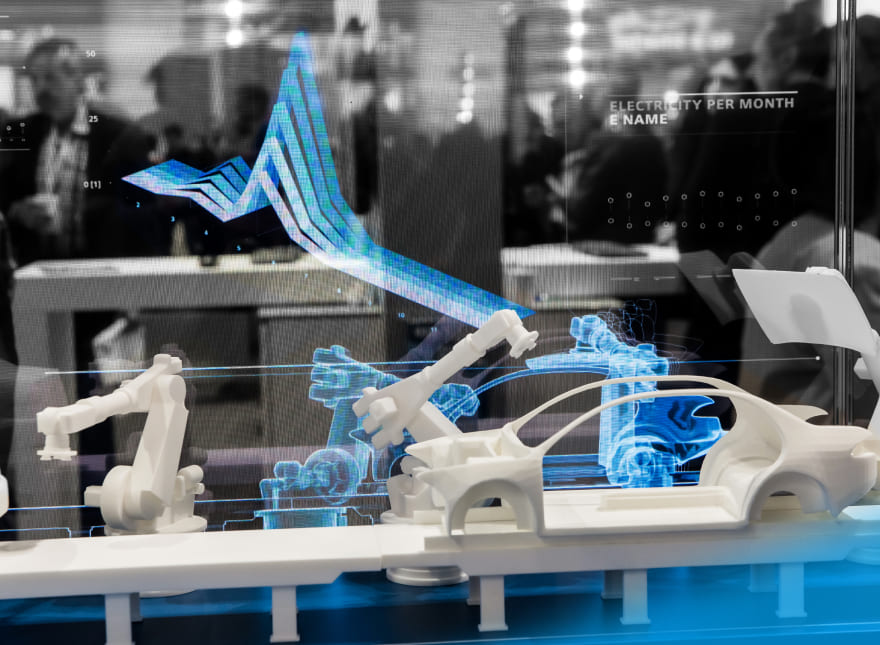
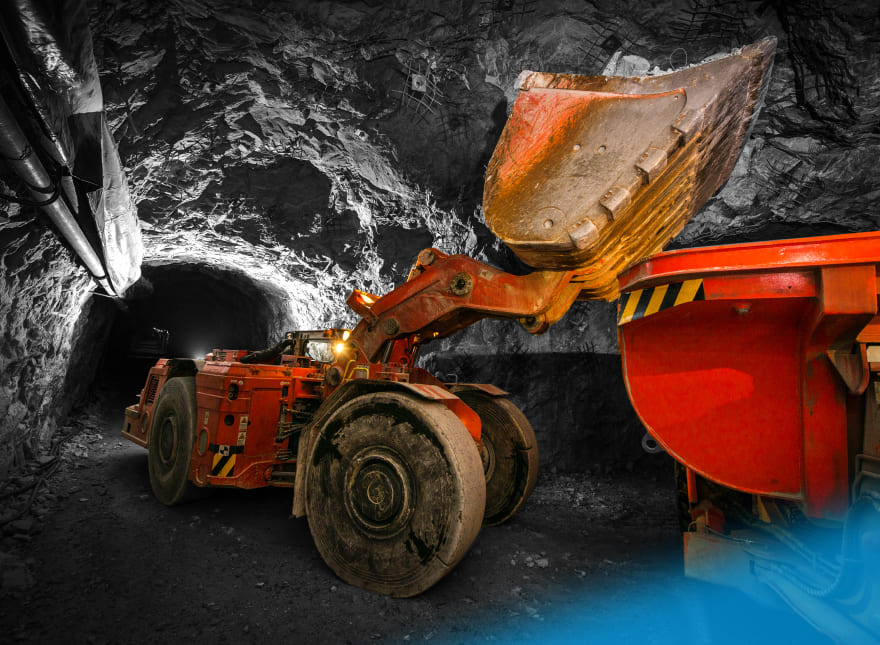
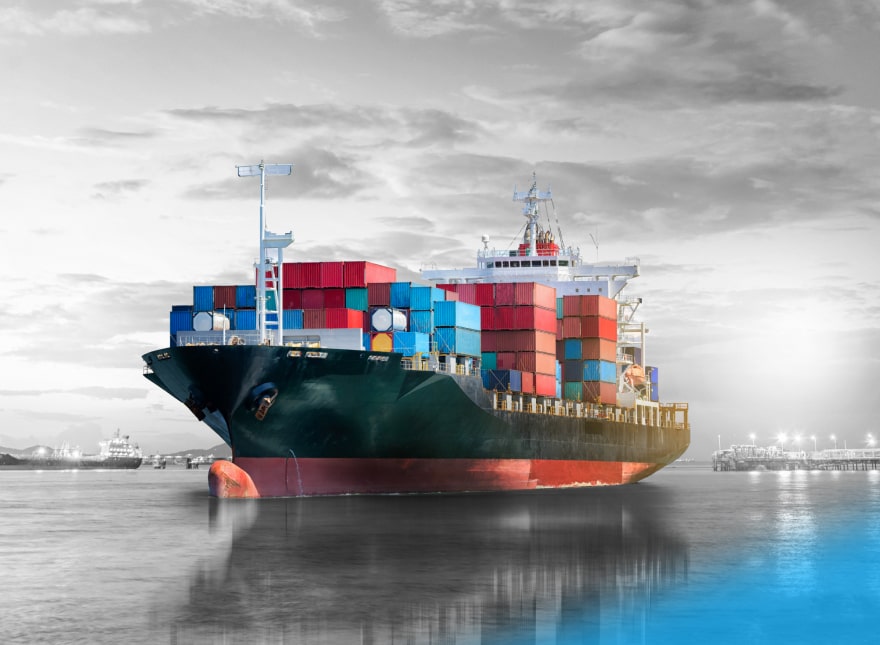