70% of global electricity is consumed by industrial machines, often inefficiently. Optimizing these processes can significantly cut costs and reduce environmental impact. Here are four ways industrial IoT energy management can help.
Industrial IoT Energy Management Scenarios
The Industry 4.0 era is an opportunity to make production more efficient. For example, industrial manufacturing solutions allow manufacturing and mining companies to predict how much energy they will need and then find ways to reduce it. This optimization typically has two levels or stages:
- It all starts with sensor-based monitoring. Sensors collect data on velocity, temperature, and humidity from energy equipment and send it to the cloud in real-time. This enables energy providers to track spikes and voltage changes remotely while monitoring asset health and planning repairs. Energy users can plan their power consumption and machine use more wisely. Overall, IoT monitoring helps both providers and users make informed decisions based on the collected data.
- Artificial intelligence enhances sensor-based monitoring by processing data, generating insights, and making predictions. Firms can forecast breakdowns, and AI-powered software helps prevent incidents. For users, AI predicts future energy needs and reduces waste, often making decisions autonomously.
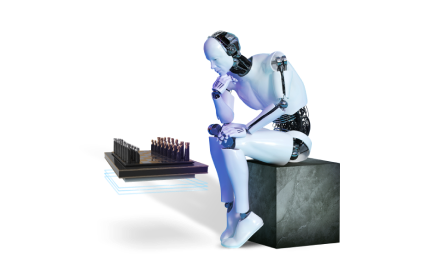
You can enhance IoT-based solutions with advanced tech, such as:
- Computer vision cameras: Monitor equipment 24/7 and use advanced AI to detect failures faster than humans could.
- Self-piloted drones: Access hazardous or remote sites to monitor equipment that would otherwise be impossible or impractical to continuously monitor.
- Digital twin models: These perfectly accurate, digital replicas of complex equipment simulate optimization scenarios and predict outcomes. They tell operators exactly how long equipment will last before it breaks down, and provide solutions to enhance the lifespan and energy efficiency of machinery.
Managing energy with IoT is essential and trending due to rising concerns about carbon footprints. IoT energy monitoring promotes sustainability while reducing operating expenses, leading to increased adoption in the coming years.
Let’s take a look at the most promising application areas of industrial IoT energy management.
Use Case 1. Regulating Air Flow with Ventilation on Demand
In mining, proper ventilation is crucial due to equipment emissions in confined spaces. However, ventilation can account for up to 40% of the total energy consumption of a mining operation. The ventilation-on-demand (VoD) system addresses this by providing the right air quality and quantity as needed. It uses tags to locate personnel and equipment, and sensors to measure airflow. The system then adjusts ventilation where needed and can schedule airflow for different mine areas.
While traditional systems ventilate the entire mine, including areas that don’t function, the VoD system can direct air only where and when it’s needed. Such optimization results in much lower electricity use for mining companies and reduced CO2 emissions.
Real-Life Example
Newmont Corporation, the world's largest gold mining company, aimed to boost productivity and reduce energy costs at their Eleonore mine in Canada. Partnering with Howden, they installed a VoD system, automating ventilation across 30 monitoring stations with flow and gas sensors.
Workers and vehicles use RFID tags for location tracking, allowing the VoD software to ensure optimal air supply in occupied zones. This system cut underground ventilation costs by half and surface ventilation by 73%, while improving working conditions with optimal fresh air for all employees.
Benefits
- Cutting electricity costs by half
- Meeting regulations to reduce CO2 emissions
- Making the workplace safe and comfortable for workers
Use Case 2. Technical Maintenance with Digital Twins
Technical maintenance of industrial machines uses significant energy. For example, adjusting mining haul truck valves manually is time-consuming and costly. Sensors streamline this by flagging only the valves needing adjustment, saving time and money. These sensors allow for real-time health monitoring of equipment.
Digital twin models use data from motion, temperature, and spatial sensors to create virtual replicas of equipment. Machine learning software quickly detects anomalies and notifies operators of potential issues. Digital twins predict when maintenance is needed, helping companies prevent problems and forecast future outcomes.
Real-Life Example
Rolls-Royce, powering over 35 types of commercial aircraft with 13,000 engines globally, uses digital twins to monitor engine operations and schedule maintenance. Onboard sensors create virtual replicas of each engine, allowing real-time health and environmental monitoring.
This technology has made engines more efficient, increasing the time between maintenance by up to 50%, reducing parts inventory, and minimizing aircraft downtime.
Benefits
- Needing to maintain equipment less often
- Reducing money spent on maintaining equipment by a third
- Saving energy on preventative maintenance services
Use Case 3. Watching Equipment with Computer Vision
Manual inspection is difficult, time-consuming, and expensive, often leading to fatigue and misclassification of defects. Human error risks factory floor machines' functionality, with costly restarts for non-stop operations.
Computer vision (CV), an AI subset, surpasses human capabilities by interpreting visual data, detecting objects, and identifying their locations. Integrated with cameras, CV helps energy companies monitor pipes and cables and identify utility service needs. CV algorithms can also detect smoke or fire on devices or power lines. Importantly, CV cameras have minimal impact on the existing infrastructure and can cover large areas.
Real-Life Example
Aramco, a Saudi Arabian petroleum and natural gas company, aimed to prevent drilling rig blowouts. Partnering with FogHorn, they implemented an edge-based computer vision (CV) solution using high-bandwidth cameras to monitor rigs in real time. Edge analytics detect potential failures with minimal latency, allowing workers to receive alerts and shut down operations if necessary.
Aramco also integrated AI into their surveillance system to detect fixed and moving assets and monitor worker safety. The system sends automatic alerts for safety guideline violations or hazards.
Benefits
- Helping engineers detect equipment failures
- Saving money on equipment repairs
- Improving safety compliance on the shop floor
Use Case 4. Monitoring Hazardous and Remote Areas with Drones
Oil and gas companies need to monitor drilling rigs, oil wells, refineries, remote offshore platforms, and miles of pipelines. These areas can be risky and often inaccessible for human workers, making equipment monitoring crucial to avoid costly downtime and energy loss.
Drones, equipped with cameras, can capture photos and videos from various angles. Machine learning software processes this visual data to reveal defects better than humans, helping oil and gas companies reduce operational costs.
Real-Life Example
The Beauly to Denny power line in Scotland spans 220 km with 615 transmission towers. Drones are used for inspection, operated by a two-person team—a drone pilot and a camera operator. The drone captures visuals while the camera operator photographs tower components. Processing software grades each component against defect standards, with results displayed on a visual asset management platform.
Benefits
- Safer and more efficient monitoring of hazardous areas
- More reliable and stable energy supply
- Additional data sources and insights on energy consumption
Bottom Line
The industrial sector has a high energy demand, but replacing old technologies with new ones can save energy. IoT energy management allows companies to control energy supply automatically and respond quickly to changing needs and prices. Advances like computer vision, drone inspections, and digital twin monitoring contribute to this, helping you:
- Save on equipment repairs and maintenance
- Reduce risks of volatile energy prices and supply
- Ensure compliance with regulations
- Stay competitive globally
Contact us to make your digital transformation smooth, effective, and affordable.
More articles on the topic
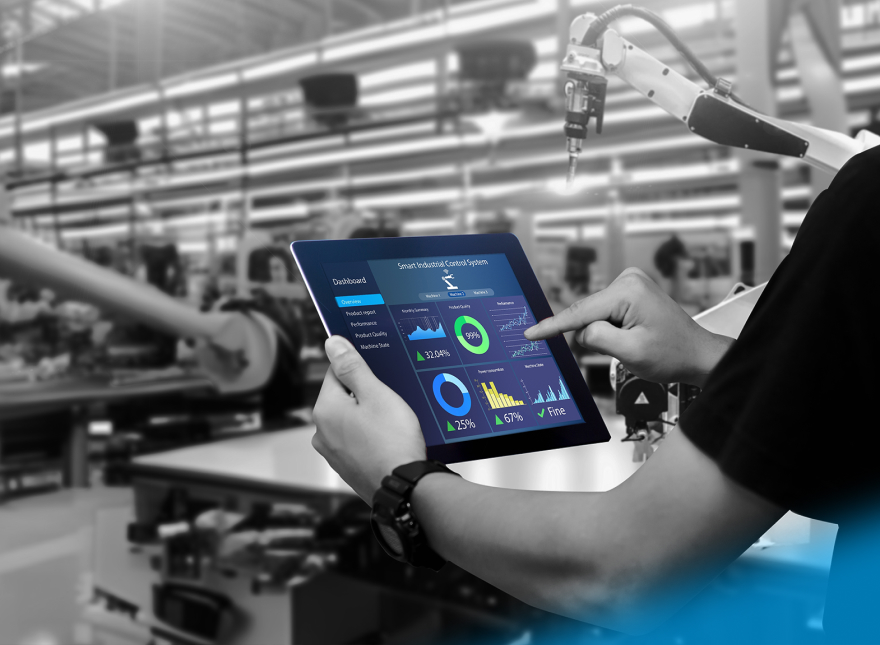
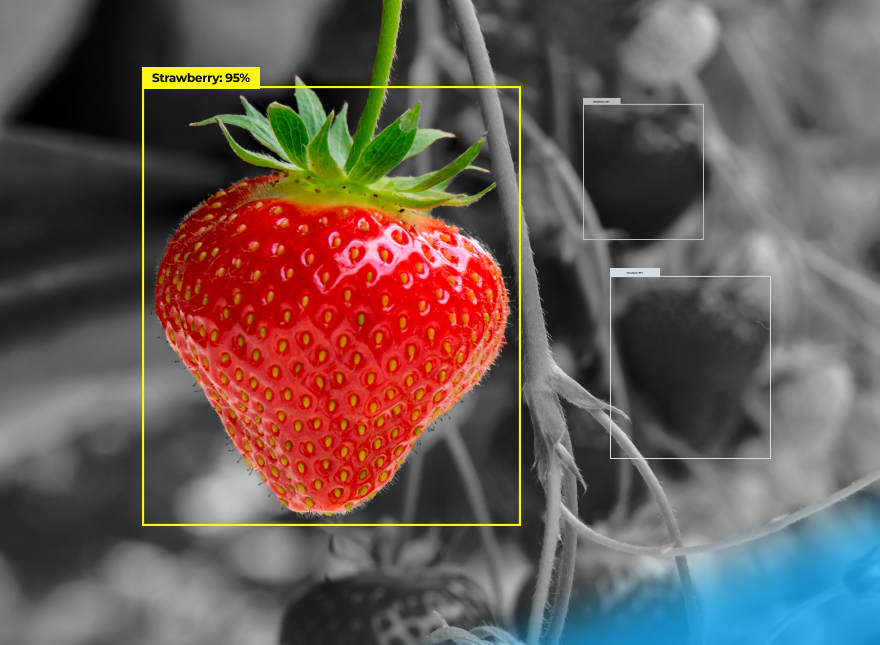
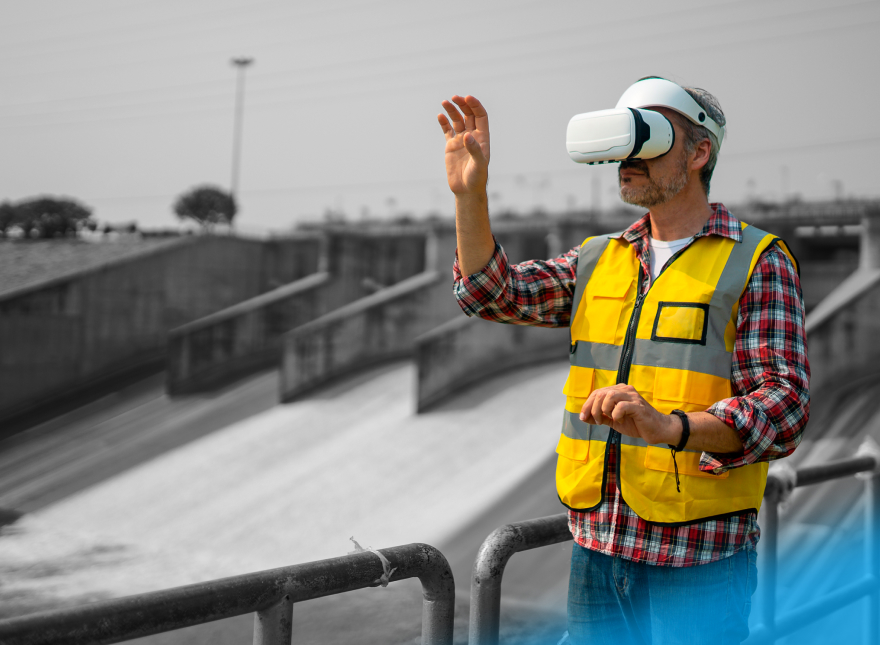
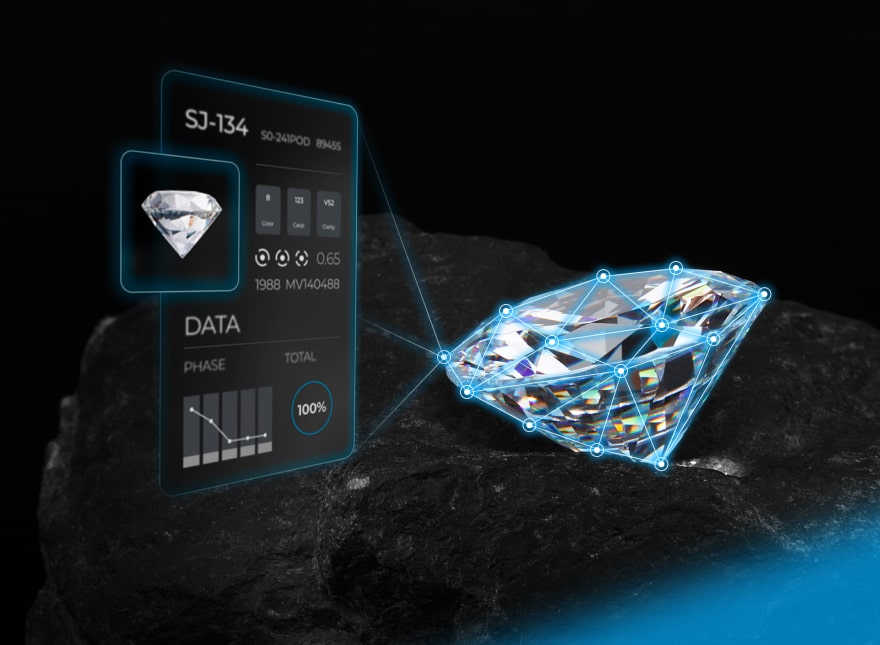
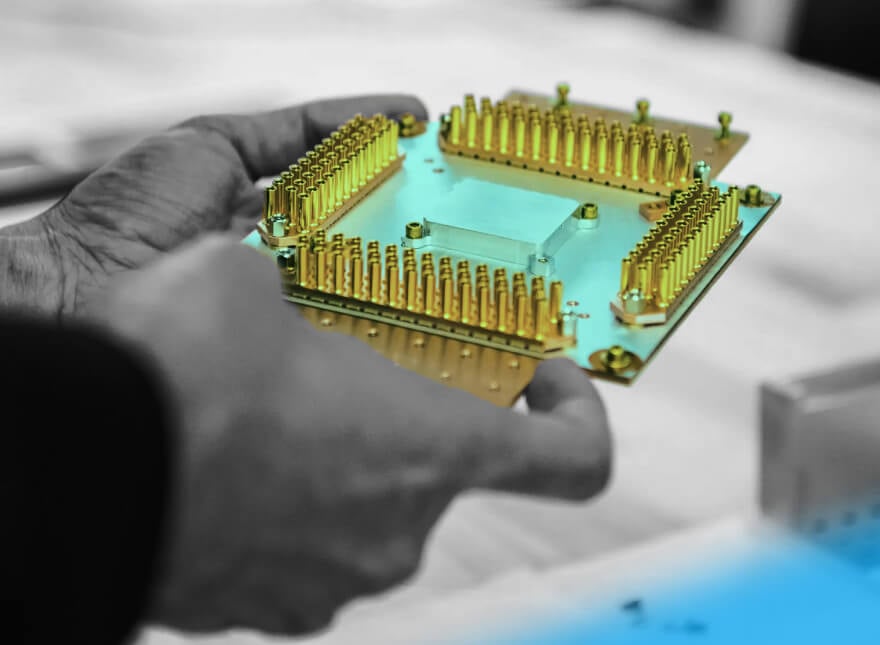
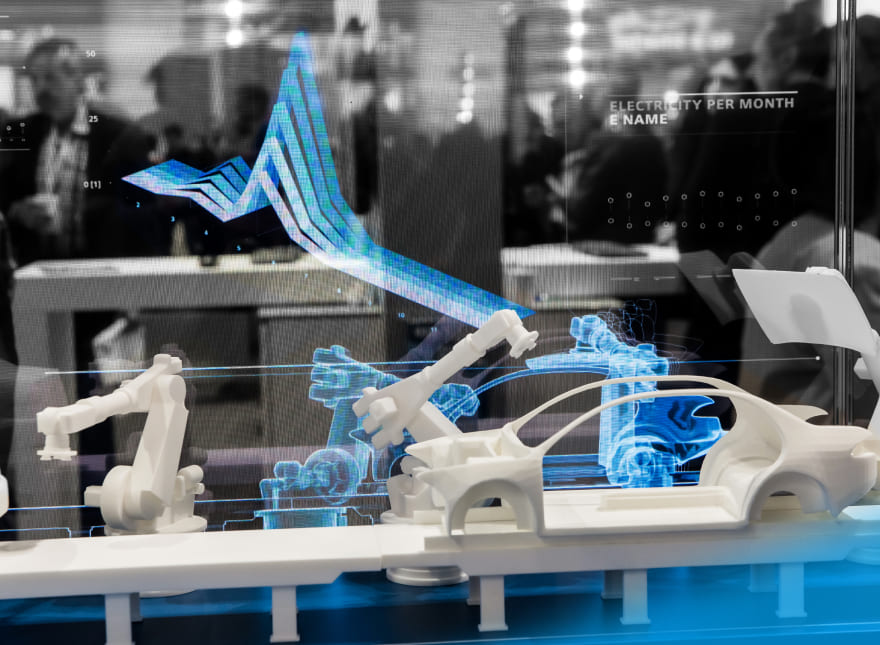