Although manual labor is still necessary in mining, AI and IoT are transforming the industry, and their impact extends beyond just automation.
As mines transition to digital platforms, they are streamlining operations, reducing errors, cutting costs, and driving better business outcomes as a result. Yet, many companies are missing out on these advantages by sticking to outdated technologies.
- Less than 5% of mines have fully embraced wearable technology.
- Only 20% have fully integrated drones into their operations.
The same trend applies to cutting operational costs. McKinsey forecasts that by 2035, AI and IoT could save the industry up to $390 billion annually. But here's the kicker: despite these potential savings, a study with 100 global mining companies found that only half of them are tapping into IoT's cost-saving opportunities. The other half? They're leaving money on the table.
Applications of AI and IoT in Mining
Companies that are implementing AI and IoT solutions are reaping the rewards and getting ahead of the competition. Keep reading to explore some of the many success stories on preventing downtime, eliminating maintenance issues, and reducing energy consumption.
Preventing Downtime in Mines with AI and IoT
Mining operations guzzle significant amounts of resources, accounting for a hefty 10% of global energy consumption. Any hiccup or shutdown comes with a hefty price tag. To dodge these pitfalls, engineers are outfitting mining machinery with sensors. These sensors feed real-time dataโcourtesy of RFID tags, sensors, and labelsโstraight to the cloud for analysis.
This analysis gives engineers insights into every facet of the mining process. Armed with this intel, they tweak operations to trim energy waste, prevent downtime, and keep production humming.
Real-Life Example: Keeping Tabs on Underground Operations
Newtrax, a global leader in IoT for underground hard rock mines, rolled out its telemetry system to a Canadian mine operated by Glencore, a major mining company. Glencore's biggest headache? The long haulage distances for trucks ferrying ore from the mine. They aimed to optimize operations by maxing out each truck's payload.
After implementing the Newtrax system, Glencore engineers monitored individual equipment's production times and calculated ore haulage utilization and loads per cycle. The result? A massive boost in efficiency and productivity.
Predictive Maintenance with AI and IoT in Mining
Historically, the mining industry struggled to foresee system failures, leading to unpredictable maintenance schedules, breakdowns, and reduced uptime. Enter predictive maintenance. Sensor networks woven into mining equipment keep a vigilant eye on operations, monitoring critical parameters like pressure, vibration, and temperature. They ping alerts before trouble strikes, enabling proactive troubleshooting and fewer financial hits for mining companies.
Real-Life Example: Streamlining Maintenance Efficiency
OSIsoft, a US-based company, revamped maintenance strategies at the Cortez Mine in Nevada. By leveraging their PI System, which crunches real-time and historical data, they shifted from a reactive to a proactive maintenance approach. The result? A sizable reduction in equipment failures and a hefty chunk of change saved each month.
Cutting Energy Consumption in Mines with AI and IoT
Tech innovations like sensor-driven valve adjustments and Ventilation-on-Demand (VoD) systems are slashing energy costs in mines. Smart sensors pinpoint valves needing adjustment, cutting down on wasted energy and saving millions. VoD systems, powered by sensors that monitor air quality and flow, fine-tune ventilation only where needed, delivering substantial energy savings.
Real-Life Example: Maximizing Energy Efficiency
Goldcorp, a top gold producer, teamed up with Cisco and AeroScout Industrial to introduce a VoD system into their mines. This smart system adjusts fan speeds based on real-time environmental data, resulting in a 50% drop in electrical consumption and a 20% reduction in costs.
The Future of Mining with AI and IoT
By embracing smart technologies to connect people, equipment, and processes, mining companies are creating transparent ecosystems that optimize operations and boost productivity.
With an experienced IoT and AI software vendor like Softeq, you can achieve similar improvements in your mining operations. Our wealth of expertise in engineering and Industrial IoT makes us the ideal partner for navigating the complexities of IoT implementation in mining. Let us help!
More articles on the topic
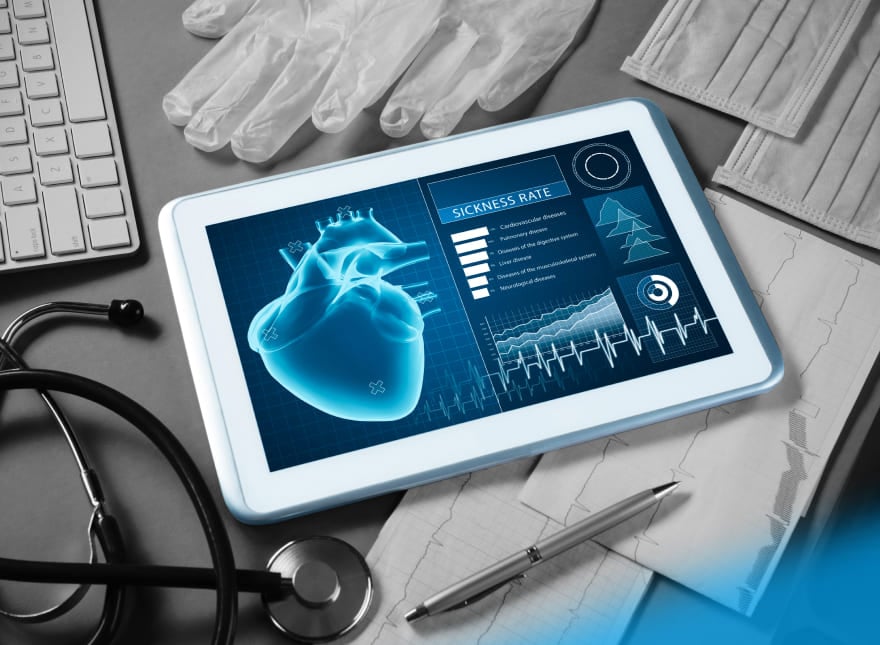
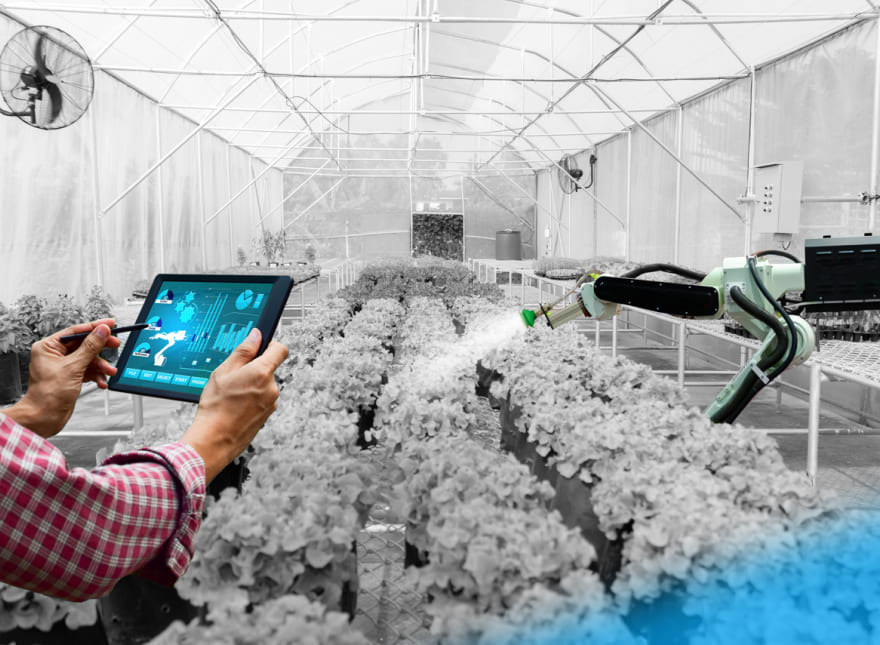
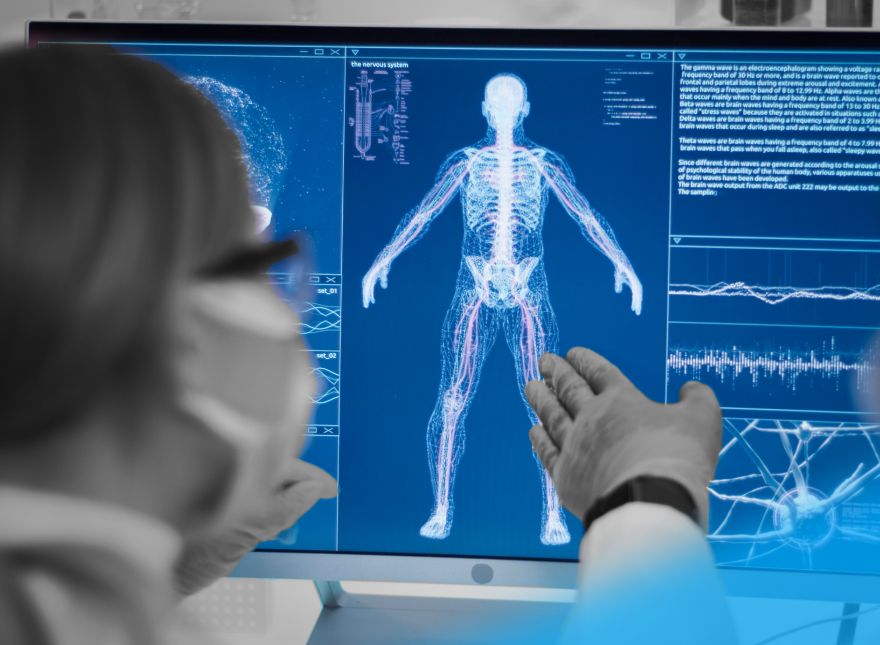
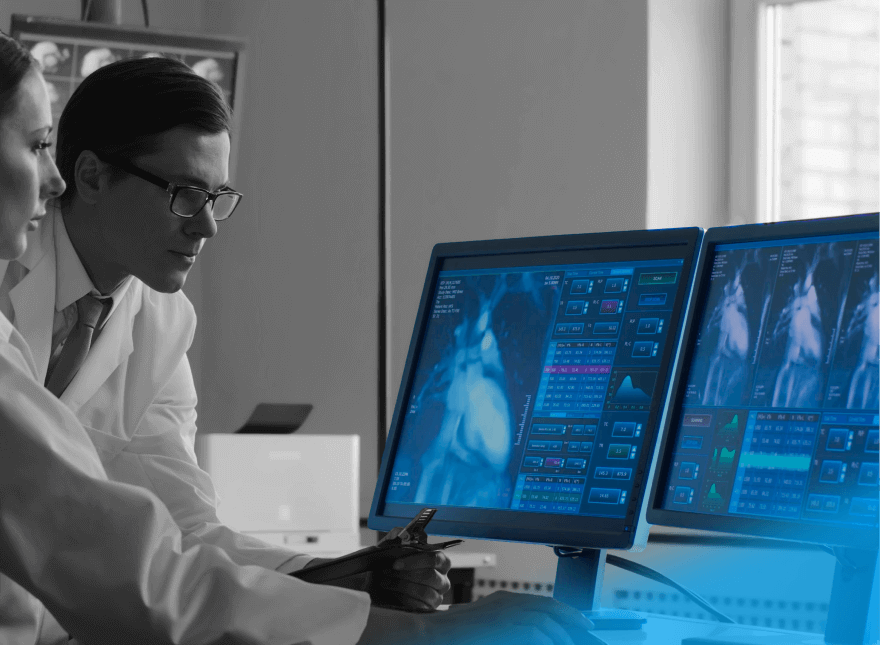
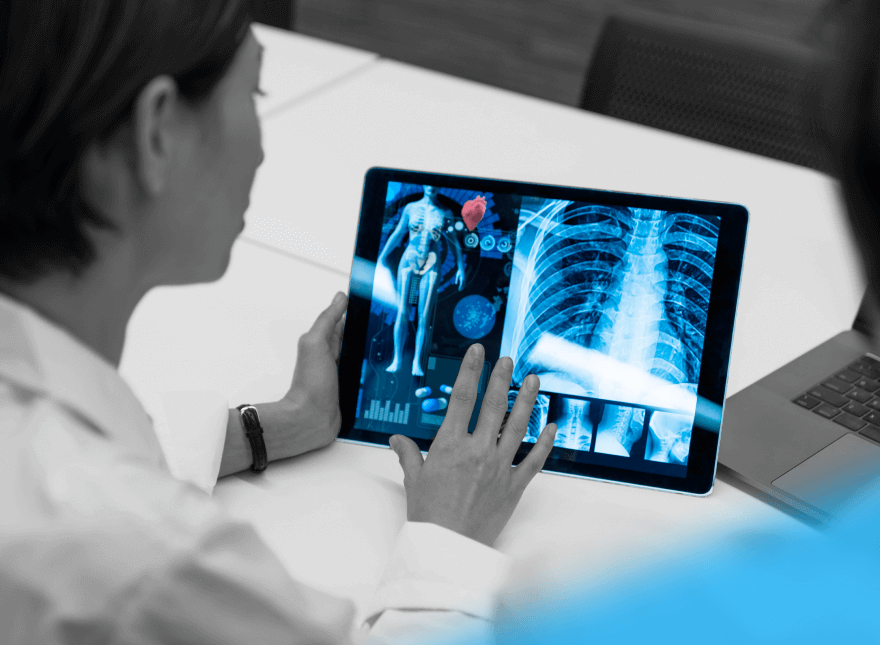
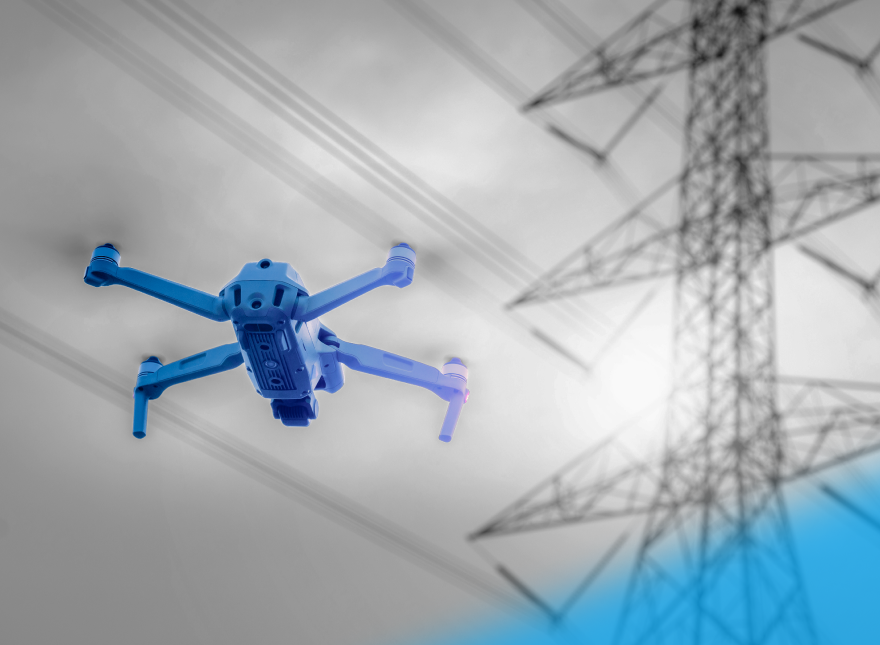