Automotive industry manufacturers are struggling to get enough chips to build their products—from airbags to navigation systems. This global electronics parts shortage is the result of several factors: pandemic-related work stoppages, increased demand, and broken transportation logistics. As a result, automotive manufacturers worldwide are expected to lose more than $14 billion in revenue in the first quarter of 2021 and approximately $61 billion for the year, as predicted by advisory firm AlixPartners.
The Causes of the Current Component Shortage
Because updating components requires complex internal checks to ensure safety and durability, automakers are often slow to do so. Keeping track of and aligning with shifts in the auto market is difficult, and meeting unexpected demand in this sector isn’t as simple as launching another production line and hiring more staff.
At the beginning of the COVID-19 pandemic, car companies assumed that the demand for cars would decrease, so they reduced their semiconductor purchases. At the same time, demand for consumer electronics rose, so semiconductor manufacturers reallocated their production.
However, soon automakers saw that their assumptions were incorrect: car demand increased. So they decided to return to their production volume plans and tried placing chip orders again. But manufacturing lines were already busy with consumer electronics orders, and switching back to automotive components would require going through the lengthy and costly process of parts revalidation. To make it even worse, prices for many components had increased 5% to 10%.
Chip shortages can be a major hurdle for car manufacturers. For startups and design houses, although they may face similar shortages, it is more easily overcome. Below you will find some useful tips for design houses on how to prepare for this challenge, based on our own experience, and practical advice for automakers to implement at large scale.
For Design Houses and Startups: How to Handle Chip Shortage
For startups and design houses working on development of new solutions, the lack of electronic components is not immediately crucial. The design process is lengthy and may take a couple of years. Even if some particular automotive chips are temporarily not available in production volumes on the market, new solutions can be developed with 3-5 samples of those chips while hoping that the supply will improve before the manufacturing stage (several chip samples are always affordable, regardless of their temporary high costs). However, in some situations, the best option is chip replacement.
Here is the checklist we use as a design house to handle the issue of electronic parts shortage and adjust component supply:
- Develop your supply network
Design houses usually have established contacts with chip manufacturers and chip vendors with whom they directly deal. With those established contacts, they can quickly find necessary products for their customers or diversify manufacturers if needed, as the price is not of a high priority for them.
- If there is shortage, design for the future market state
As the design process takes at least a year, startups and design houses may create solutions with just several chip samples. When the process is over, the chip shortage will likely be over as well, and there will be the required chips in the volume required for manufacturing.
- If there is no shortage, plan in advance to pre-see it
When planning a new product, the smart thing to do after the BA stage is selecting the chipset for the product—at the very beginning of the project. Then you should proceed straight to issuing a purchase order for stocking parts for the mass production. It should be done well in advance, preferably before even beginning development work. To solve this task, hire an engineering team competent in:
- chip capabilities
- the range of specs for the project
- writing the firmware and building connected apps/software.Remember, car makers preferring a just-in-time ordering approach are moved to the back of the line for future chip shipments.
- Failure story: What may happen if you don’t do this
Imagine: a product developer has all the necessary integrated circuits for a design. But at some point, he or she fails to lock up inventory for one simple discrete component. The lack of availability of a specific critical capacitor shuts down the production line. And the result? The part is now back-ordered for 52 weeks.
- Initiate temporary chip replacement
Replacing chips is the first and simplest solution for designers: just choose a chip from the same manufacturer, in the same family, with a larger memory than needed. Or choose a chip with less memory and trim down the firmware code as necessary. Consider designing the circuit to accommodate different package styles. For example, the circuit board and logic might be designed for either a 10-pin chip or a 16-pin chip—whichever is available. It may mean fewer features but will still be sufficient for launching an MVP.
- Redevelop the solution
Chip shortages are not the only possible cause of chip replacement. If a chip is taken out of production or has been outdated, engineering teams can also redevelop the solution so that it can be paired with an available chip.
Thus, the procedure of chip replacement at the design stage is quite standard and requires technical expertise, but not large budgets. You can always turn to our engineering teams for consultations or solution development.
For Car Makers: How to Overcome Chip Shortages
Manufacturing may require millions of chips, and here the global electronic components shortage becomes a true challenge. Consider the following practicalities to mitigate problematic lead times:
1) For existing products
- Design around the shortage
There is no right or wrong way to design an electrical circuit: there are only more or less efficient designs. Creative engineers can always modify the schematics to develop around the lack of a critical component. The question is the balance between costs and design efficiency. For example, even old-school analog circuits can perform the tasks of some simple microchips, but they will be much less compact. The smaller is the chip, the more expensive it is.
- Leave your options open
Same as design houses and startups, car manufacturers can also find themselves in situations where no applicable chip sample is available and chip replacement becomes necessary. In this case, a manufacturer should choose the same batch chips with smaller or higher output capacity that are suitable for the development stage. If designed properly, the device may function but with fewer features. It is always better to ship a de-featured product than no product at all.
2) Security Tips
- Avoid the grey area
The grey market is made up of unofficial channels and suppliers who purchase an electronic component for resale on the “spot” market at significantly higher prices. Many are legitimate, but use caution when sourcing components from grey market sellers. This might be a viable option for a shorter run, less price-sensitive, or broad quality tolerance products. However, the grey market is notorious for lack of batch control, quality control, and even mixing in counterfeit chips of lower quality and lesser tolerance specs.
- Avoid the danger zone
Counterfeit chips may serve as a cyber-attack vulnerability vector. Such compromised chips are a serious problem for the semiconductor, automotive, and consumer electronics industries. For example, a counterfeit chip in a tank could feed details of the payload to adversaries. Rogue code in a fake semiconductor could shut down the air supply of an airliner. A counterfeit chip could be used to shut down a car in a ransomware attack. More on this topic can be found here.
3) Continuous Supply
- Be aware of terms and conditions
Most chip suppliers have changed their terms and conditions of sale: they have moved to 90-day cancellation lead times instead of the typical 30 or 45-day terms. Consider this issue when thinking of double or triple booking orders from different suppliers. You might get stuck holding a lot more inventory than you need at some point. - Join preferred programs
Semiconductor companies like Microchip are offering Preferred Customer Programs to guarantee deliveries beyond six months. These preferred programs require a long-term commitment to the vendor—often a year or longer.
Wrap-up
Since the production of modern cars relies on hundreds of computer chips, the automotive industry should have flexible and agile supply chains. This will help meet unexpected changes in demand and supply and increase resilience.
More articles on the topic
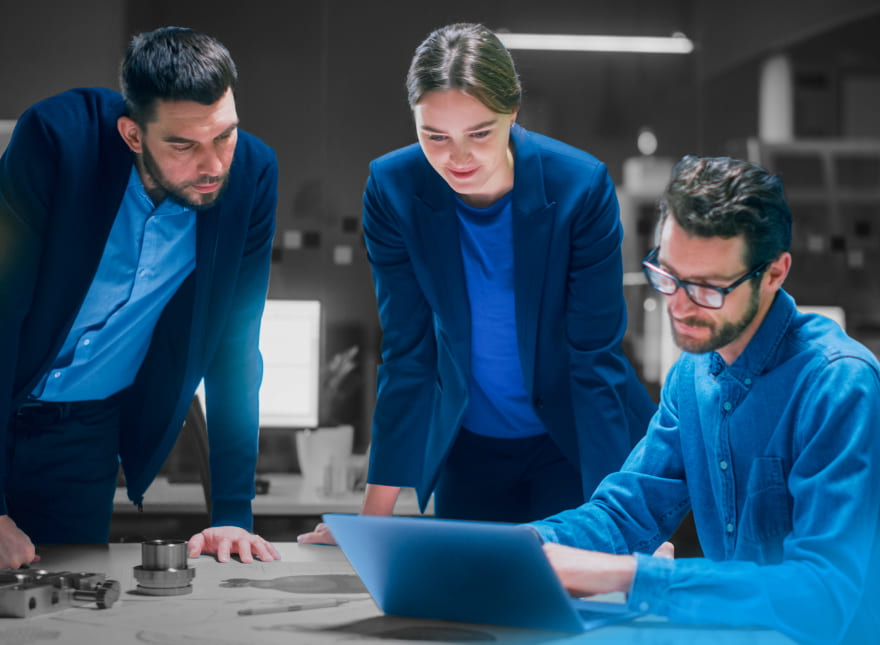
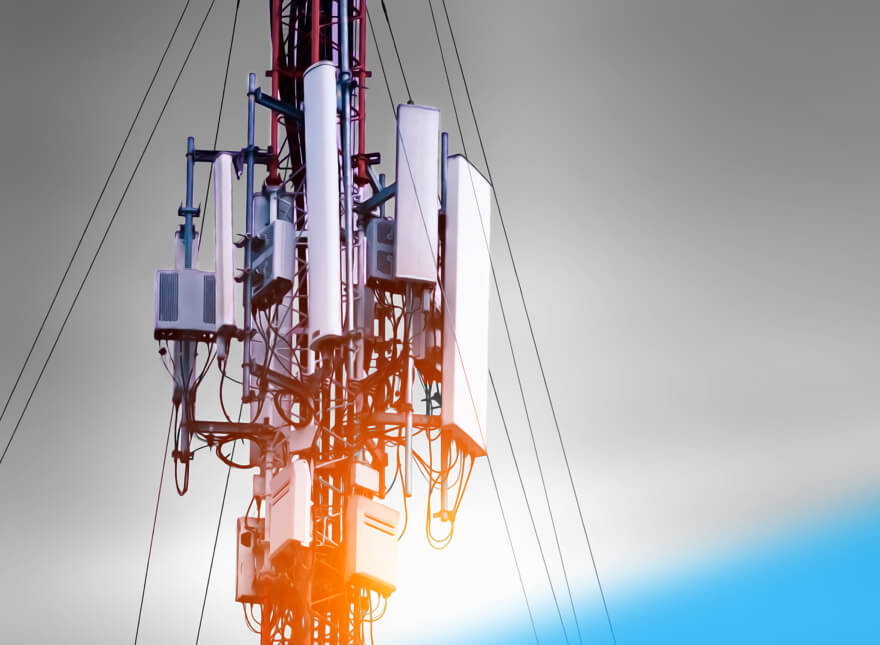
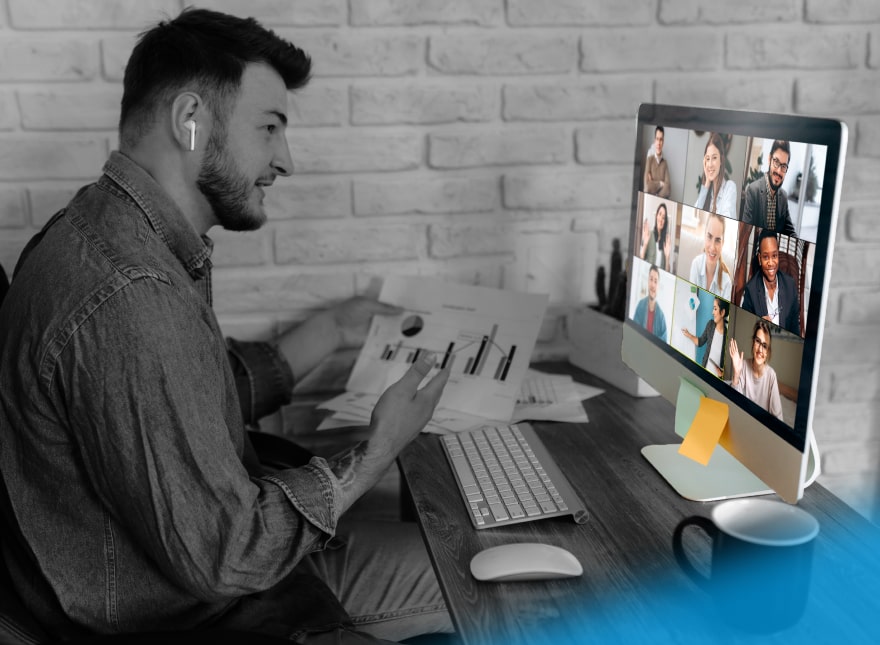
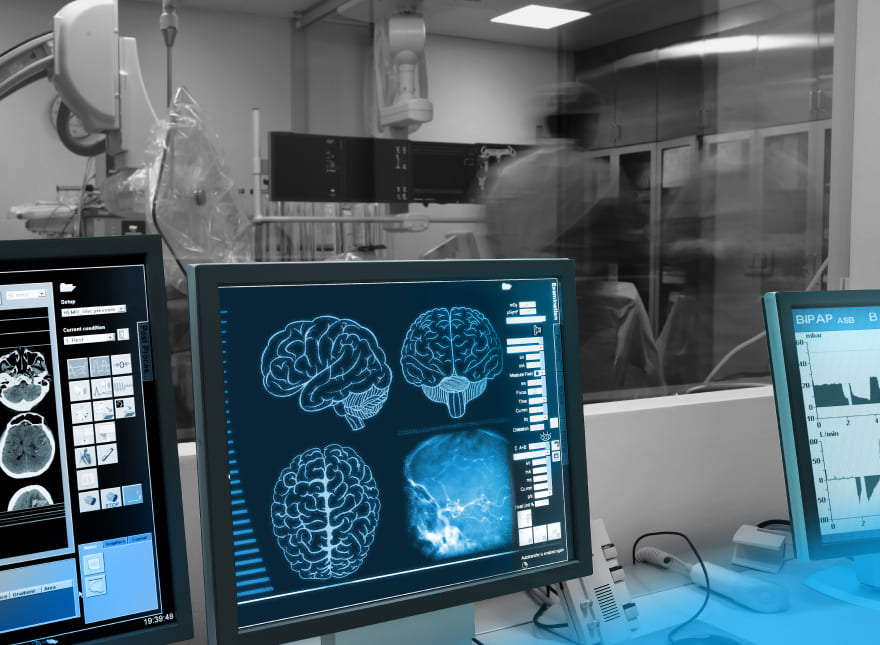
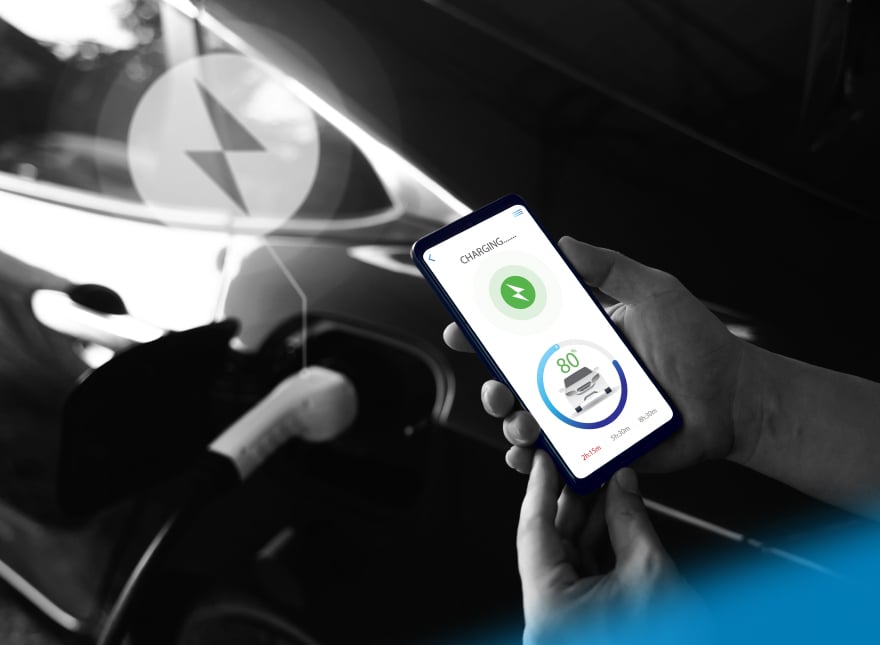
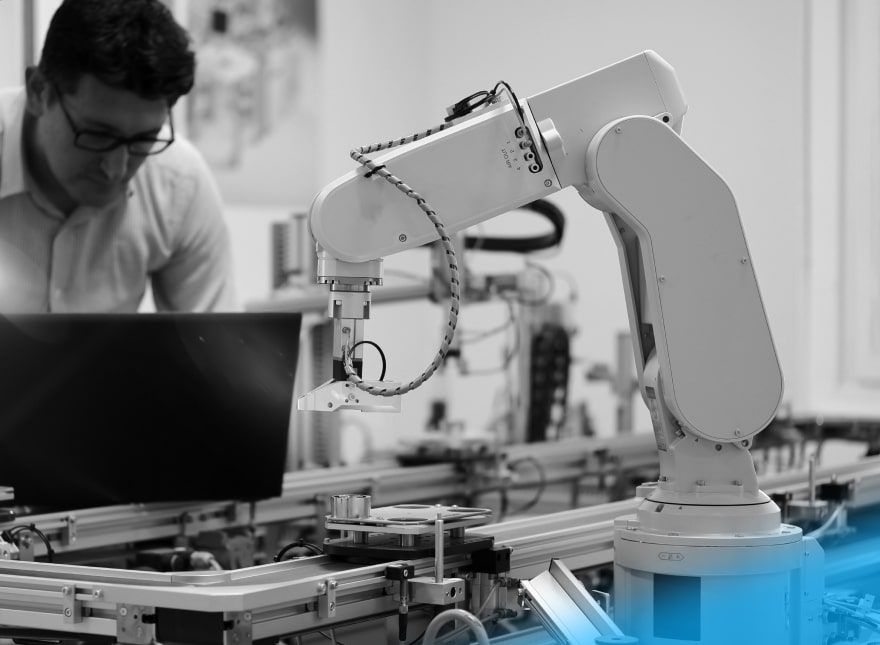